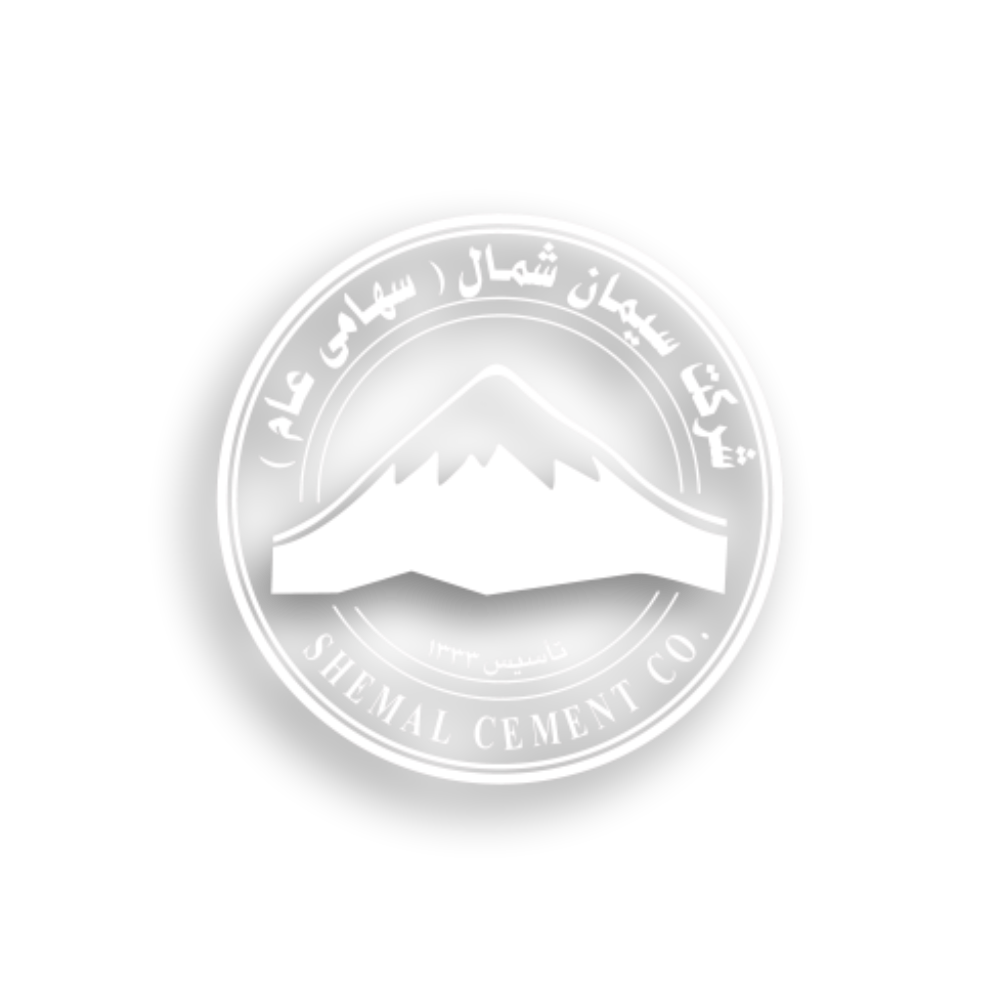
شرکت سیمان شمال
خانه / محیط زیست / گزارش تعميرات الكترو فيلتر سيمان چهار
گزارش تعميرات الكترو فيلتر سيمان چهار
مجری پروژه: واحد محیط زیست
فروردین ماه ۱۳۹۷
مقدمه
انتشار گردوغبار و ذرات سیمان یکی از مشکلات بزرگی است که کارخانجات سیمان با آن روبرو هستند. امروزه با توجه به قوانین سختگیرانه زیست محیطی هرگونه تخطی از استانداردهاي مصوب منجر به برخورد شدید و جلوگیري از ادامه فعالیت واحد تولیدي میشود. گردوغبار در یک کارخانه سیمان در اثر سایش، خردایش، تخلیه و جابجایی، پخت مواد و … تولید میشود. ذرات سیمان، به دلیل خواص فیزیکی و شیمیایی، میتوانند توسط سیستمهاي کنترلی از جمله فیلترهاي کیسهاي، سیستمهاي هیبریدي و الکتروفیلترها بازیابی شده و ضمن جلوگیري از انتشار در محیط، مجددا در فرآیند مورد
استفاده قرار گیرند. در حال حاضر با توجه به قدمت بالاي خطوط ۱ و ۲ تولید سیمان در شرکت سیمان شمال به دلیل آلایندگی زیست
محیطی و راندمان پایین از چرخه تولید خارج شده و تنها خط تولید شماره ۳ مشغول به تولید میباشد. وضعیت فعلی سیستمهاي غبارگیر خط تولید سه به شرح زیر است:
الف: بگ هاوسها: خط تولید ۳ مجموعا داراي سه دستگاه بگهاوس جتپالسی در دپارتمانهاي آسیاب مواد، گریت کولر و آسیاب سیمان پنج است.
ب: الکتروفیلترها: خط تولید ۳ مجموعا داراي دو دستگاه الکتروفیلتر در دپارتمان هاي کوره و آسیاب سیمان چهار است.
ج: بگفیلترهاي جتپالسی و مکانیکی: خط تولید ۳ مجموعا داراي سی و نه دستگاه بگفیلتر است که از این تعداد بیست و چهار دستگاه به صورت جتپالسی، چهار دستگاه به صورت مکانیکی-ویبراتوري و یازده دستگاه به صورت مکانیکی-چکشی میباشند.
از بین دو دستگاه الکتروفیلتر مشغول به کار، الکتروفیلتر کوره به دلیل حساسیت بالا و خروج حجم بالایی از گازها و غبار خروجی و عدم تأمین حداقل استانداردهاي جدید مصوب، در برنامه تغییر سیستم و تبدیل به بگهوس قرار گرفته است که بزودي عملیات اجرایی آن آغاز خواهد شد. ولی الکتروفیلتر سیمان چهار فعلا پاسخگوي نیاز بوده و در صورت عملکرد بهینه توانایی کنترل غبار خروجی را دارا میباشد. این الکتروفیلتر به جهت عمر بالا و عدم انجام تعمیرات اساسی بر روي آن دچار مشکلاتی بود که منجر به عدم غبارگیري مطلوب آن شده بود. لذا پروژه تعمیرات اساسی الکتروفیلتر سیمان چهار با تکیه بر دانش و توان داخلی شرکت تعریف شده و طبق یک برنامه زمانبندي دقیق در فروردین ماه سال
۱۳۹۷ به نحوي اجرا گردید که کوچکترین خللی در برنامه تولید و فروش شرکت پدید نیاید.
طرز کار الکتروفیلتر
عامل اصلی غبارگیری در الکتروفیلترها ایجاد میدان الکتریکی و باردار کردن ذرات غبار و نشست آنها بر روی صفحات جذب و در نهایت تکاندن صفحات و هدایت غبار جمع شده به داخل هاپر خروجی میباشد. لذا هر دستگاه الکتروفیلتر شامل بخشهای اصلی به شرح زیر طبق شکل (۱) میباشد:
- الکترودهای دیسشارژ (Discharge Electrode)
- صفحات جذب غبار (Collecting Plate)
- سیستم ضربه زن (Rapping System)
- سیستم جمع آوری و تخلیه (هاپر، روتاری و مارپیچ) (Hopper, Rotary, Screw)
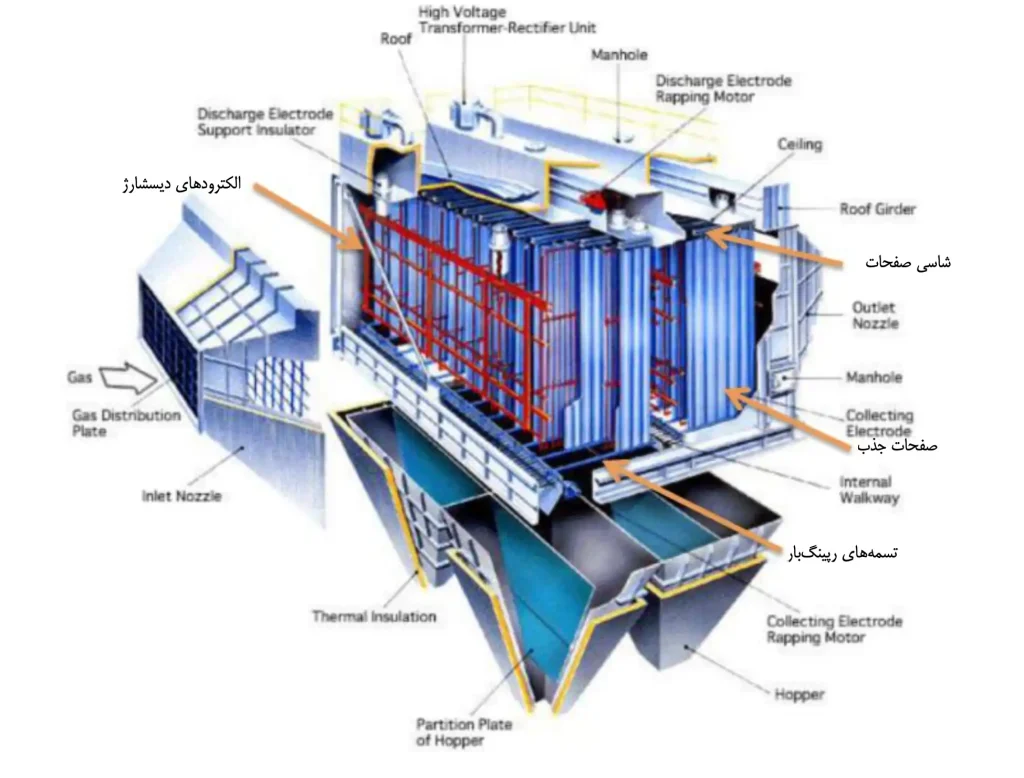
مشخصات فنی الکتروفیلتر سیمان ۴
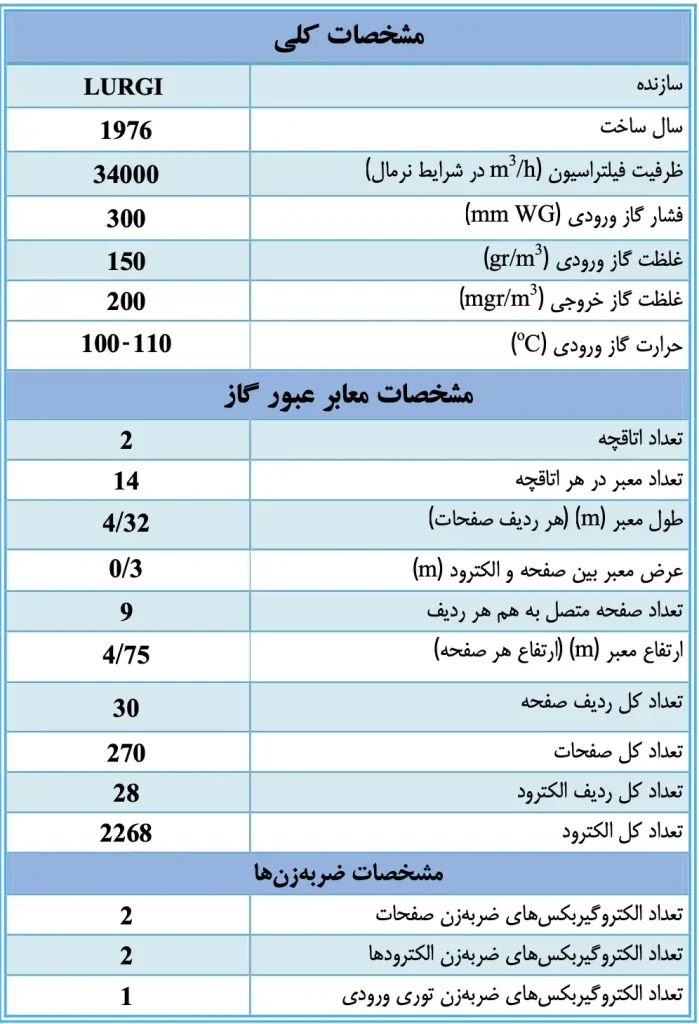
برنامه زمان بندی تعمیرات اساسی الکتروفیلتر
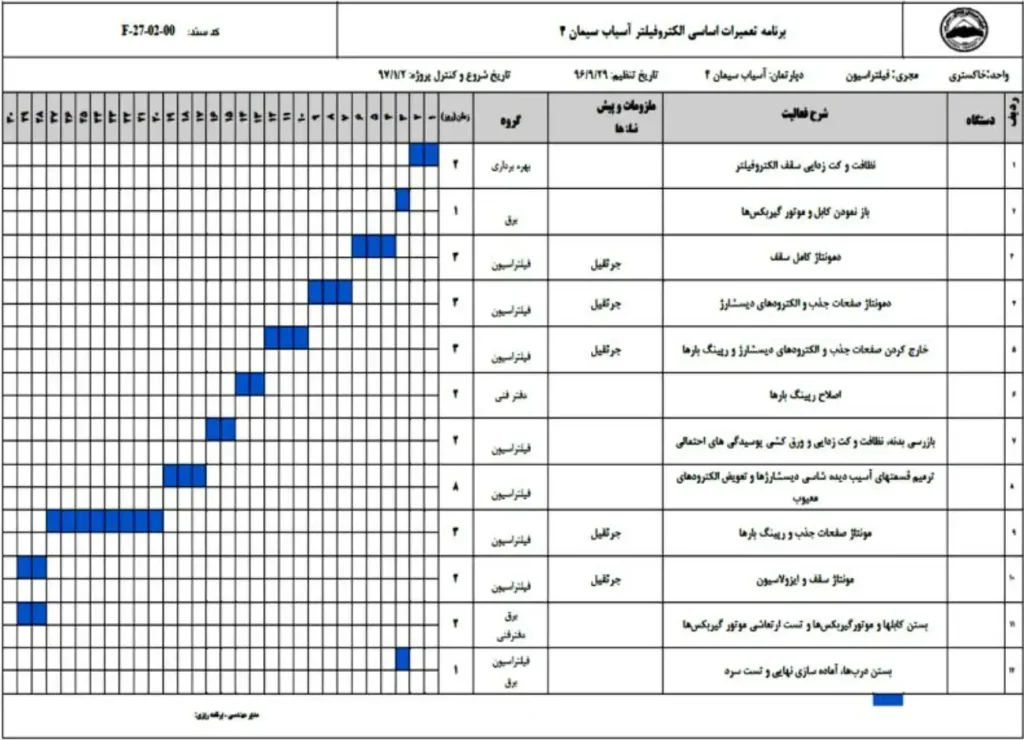
مجری پروژه و همکاران:
مجري اصلی اجرای این پروژه واحد محیط زیست شرکت سیمان شمال بود که با همکاری واحدهای دفتر فنی (قسمت طراحی مهندسی، کارگاه تراشکاری و آهنگری ( ترانسپورت ) جرثقیل، تاور و لیفتراك(، برق و بهرهبرداری )نظافت ) طبق برنامه زمان بندی پروژه انجام گردید.
تاریخ شروع و پایان:
به منظور جلوگیری از اختلال در روند تولید و فروش محصول تصمیم گرفته شد از فرصت تعطیلات عید نوروز و کاهش فروش معمول در ماه فروردین استفاده شده و پروژه در تاریخ ۹۷/۱/۲ آغاز به کار گردید. طبق زمانبندي یک ماهه انجام شده و با احتساب چند روز تعطیلی آخر هفته، کار در تاریخ ۹۷/۲/۵ به اتمام رسید.
نیروی انسانی:
طبق برنامه و گزارش عملکرد پروژه حدود ۲۸۰۰ نفر-ساعت کار جهت اجرای این پروژه صرف گردیده است که تمامی آن توسط پرسنل داخلی کارخانه تأمین گردیده و قسمتهای دخیل در پروژه در خلال کار، وظایف جاری خود را نیز به انجام رساندهاند.
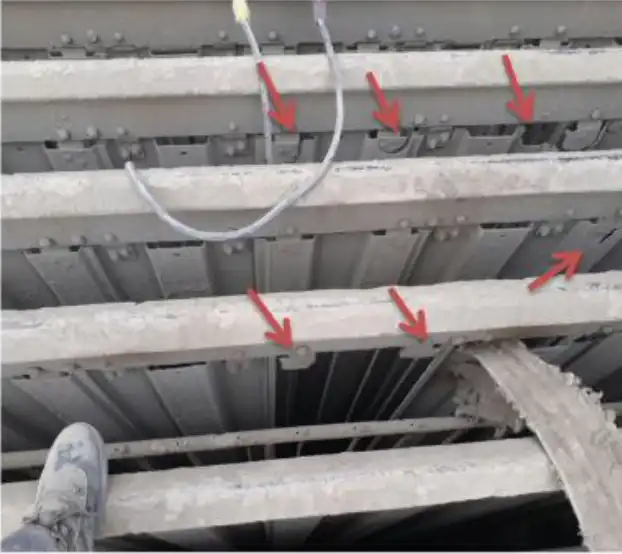
تصویر ۲. شکستگی صفحات جذب از محل اتصال به گوشواره ها
دلایل اجرای پروژه
در میان اجزای الکتروفیلتر، سیستمهای ضربه زن و جمع آوری غبار را میتوان در توقفات کوتاه مدت دستگاه مورد ترمیم قرار داد. این تعمیرات بطور مستمر بر روی دستگاه انجام شده و از این بابت مشکل خاصی وجود نداشت. لیکن در مورد صفحات جذب (شامل شاسی، صفحه و تسمه رپینگبار) و الکترودهای دیسشاژ و شاسی آن، به جهت عدم امکان دسترسی در حالت عادی امکان ترمیم و تعویض وجود ندارد. این بخشها به جهت عمر زیاد و ضربات مستمر ایجاد شده توسط سیستم ضربه زن به مرور دچار خستگی مکانیکی و شکستگی شده بودند که نوسان ایجاد شده در صفحات و الکترودهای شکسته موجب ایجاد جرقه شده و بطور مرتب عملکرد دستگاه را با اختلال مواجه میکرد که ضمن کاهش تولید، موجب آلودگی محیط زیست میگردید. تصاویر (۲) و (۳) بخشی از آسیب هاي وارد شده را نشان میدهد.
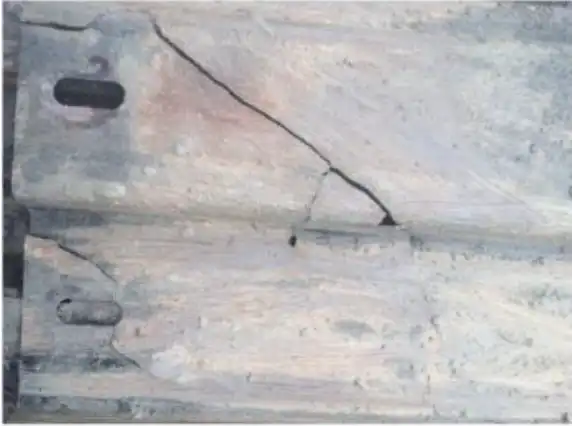
تصویر ۳. شکستگی صفحات جذب از محل اتصال به تسمه هاي رپینگبار
در حین کار دستگاه گاهی الکترودهای دیسشارژ از یک نقطه بریده میشد که نوسان آن موجب ایجاد اتصالی و توقف
دستگاه میشد. در چنین شرایطی به جهت کوچک بودن فضا، دسترسی برای تعویض الکترود مهیا نبود و تنها کاری که میشد کرد بریدن و قطع کامل الکترود بود تا اتصالی رفع شده و دستگاه راه اندازی شود. این کار به مرور راندمان غبارگیری الکتروفیلتر را کاهش داده بود. تصویر (۴) نبود دو عدد الکترود را بر روی بخشی از شاسی آن قبل از تعمیرات نشان میدهد.
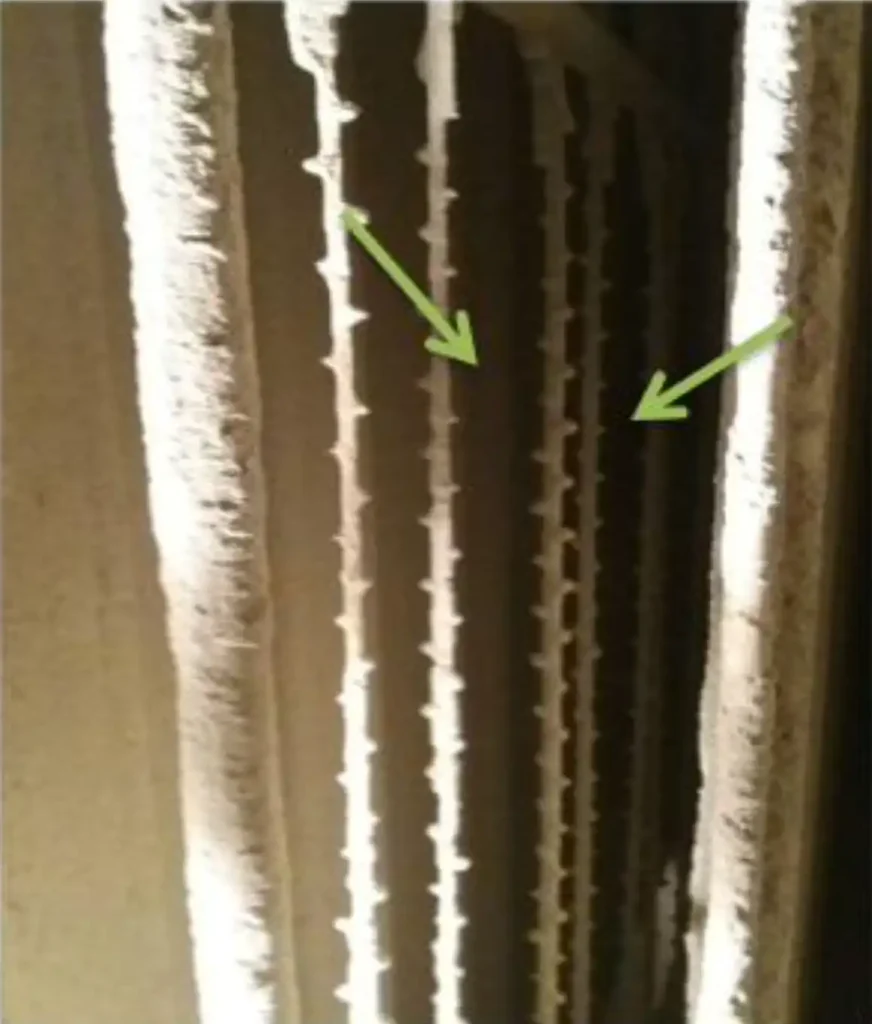
تصویر ۴. کمبود الکترودهای دیسشارژ روی شاسی
علاوه بر الکترودهای بریده شده، بخشی از الکترودها نیز به جهت تغییر شکل و در مواردی شکستگی شاسی، شل شده و نوسان زیادی ایجاد میکردند که تعویض آنها و اصلاح شاسی نیز ضروری بود (تصویر ۵).
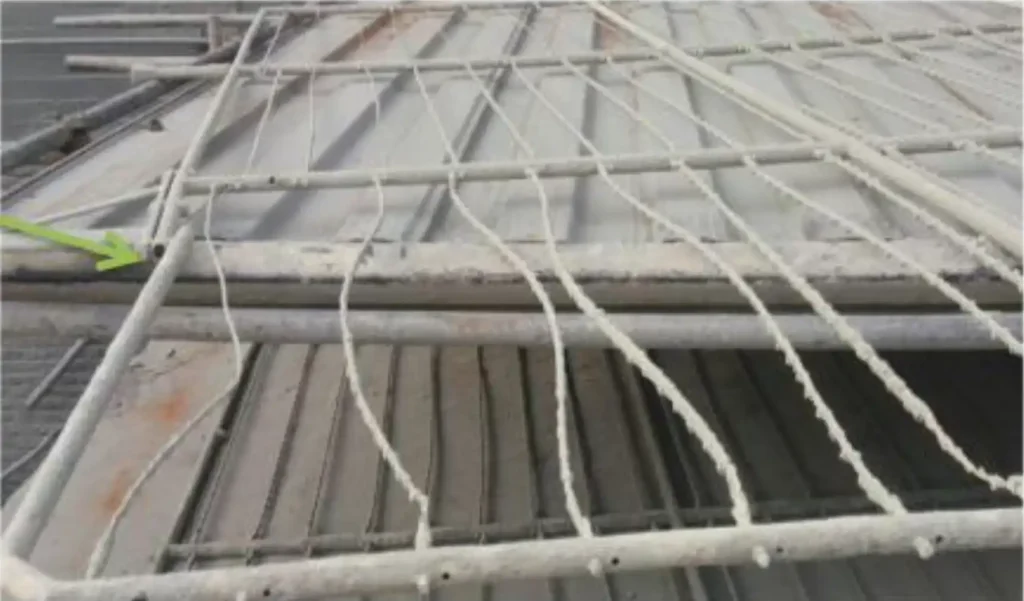
تصویر ۵. الکترودهای شل شده به جهت تغییر شکل و بعضاً شکستگی شاسی
از دیگر مشکلاتی که موجب تأثیر منفی بر عملکرد الکتروفیلتر شده بود، ایجاد لایه مستحکمی از غبار )کُتگرفتگی ( روی صفحات جذب و الکترودهای دیسشاژ بود که بدون دمونتاژ کامل دستگاه امکان نظافت آن وجود نداشت. تصاویر (۶) و (۷) بخشی از این کُتگرفتگی را نشان میدهد. همچنین ساییدگی نوکهای تیز برخی الکترودها نیز موجب کاهش کارایی آنها شده بود که این الکترودها نیز باید تعویض میشدند.
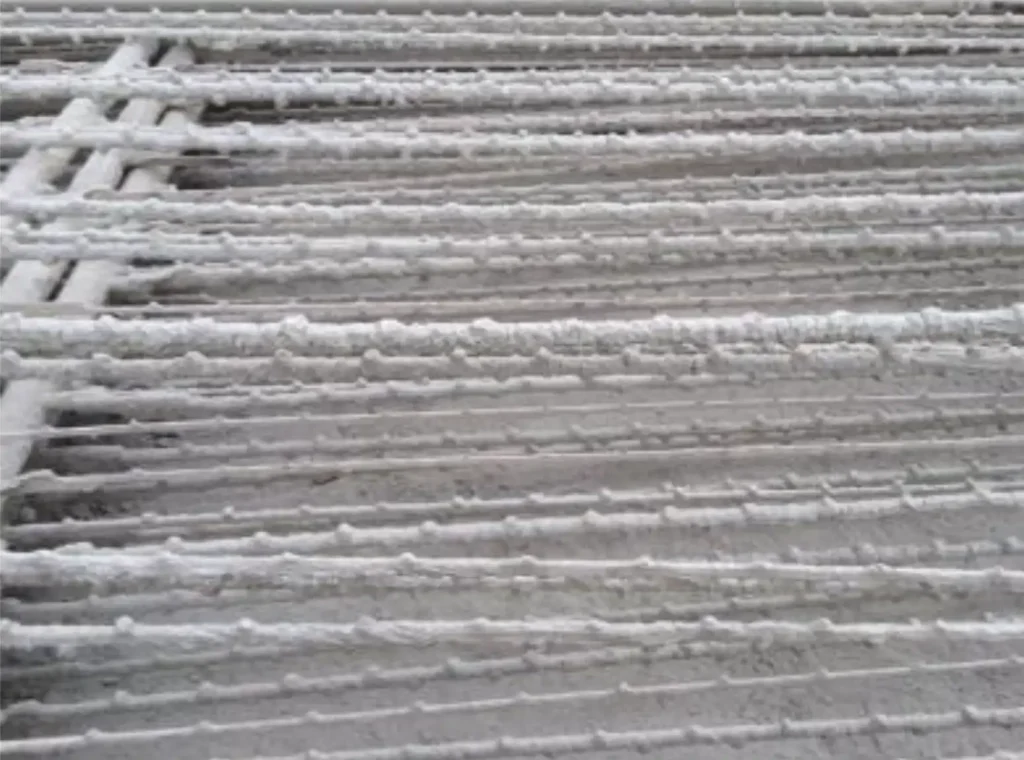
تصویر۶. کُتگرفتگی روی الکترودهای دیسشارژ
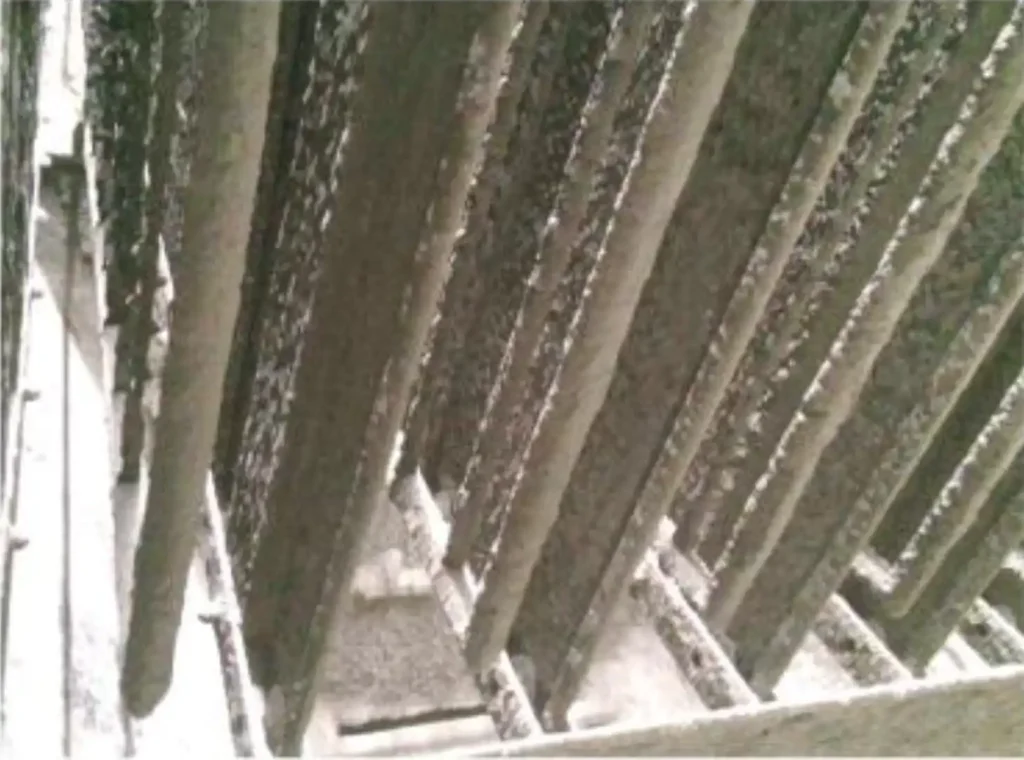
تصویر ۷. کُتگرفتگی روی صفحات جذب و الکترودهای دیسشارژ
به جهت ضربات مستمر وارده از سیستم ضربه زن به رپینگ بارها و سندانیها، این قطعات عمدتا دچار شکستگی شده و عملیات غبارگیری مختل میگردید. لذا تعویض این قطعات نیز در دستور کار قرار گرفت.
مراحل اجرای پروژه
۱. برآورد و تهیه قطعات مورد نیاز
صفحات جذب:
مهمترین قطعه مورد نیاز در اجرای این پروژه صفحات جذب بودند. بخشی از صفحات با ابعاد
مورد نظر در انبار شرکت موجود بود که مورد استفاده قرار گرفت. بخش دیگری از صفحات با طول بیشتر توسط دفتر فنی و کارگاه آهنگری به ابعاد مورد نظر بریده شد و سوراخهای مورد نظر روی آنها ایجاد گردید. تصاویر (۸) و (۹) نحوه انتقال صفحات جذب اصلاح شده توسط آهنگری را نشان میدهد. به منظور جلوگیری از تغییر شکل، صفحات بر روی شاسی مناسبی قرار گرفته و توسط لیفتراك بر روی کفی جرثقیل قرار داده شد و جابجا گردید.
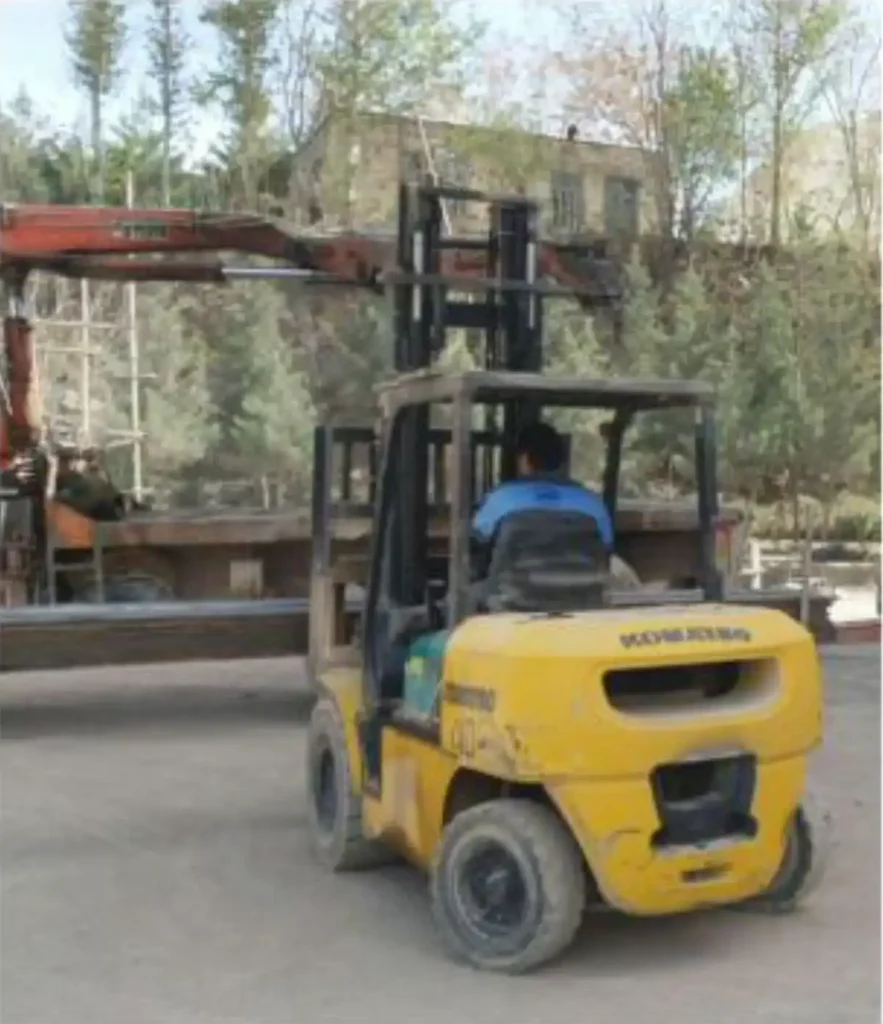
تصویر ۸. بارگیری پالت صفحات جذب بر روی جرثقیل توسط لیفتراك
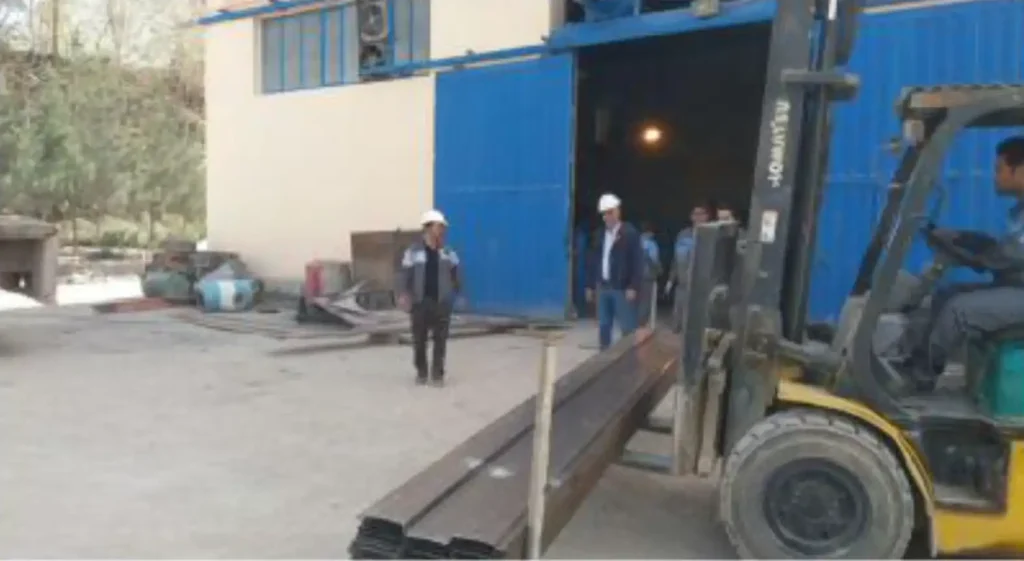
تصویر ۹. جابجایی و انتقال صفحات جذب توسط لیفتراك
الکترودهای دیسشاژ:
به جهت انبارداری طولانی الکترودهای دیسشاژ موجود در انبار دچار کُتگرفتگی و زنگ- زدگی سطحی شده بودند که قبل از شروع طرح اقدام به جداسازی الکترودهای سالمتر و خیساندن آنها در حلال مناسب (گازوئیل) گردید (تصویر ۱۰). سپس الکترودها با فرچه سیمی نظافت شد و پیچهای دو سمت الکترودها توسط حدیده مناسب اصلاح و روان گردید.
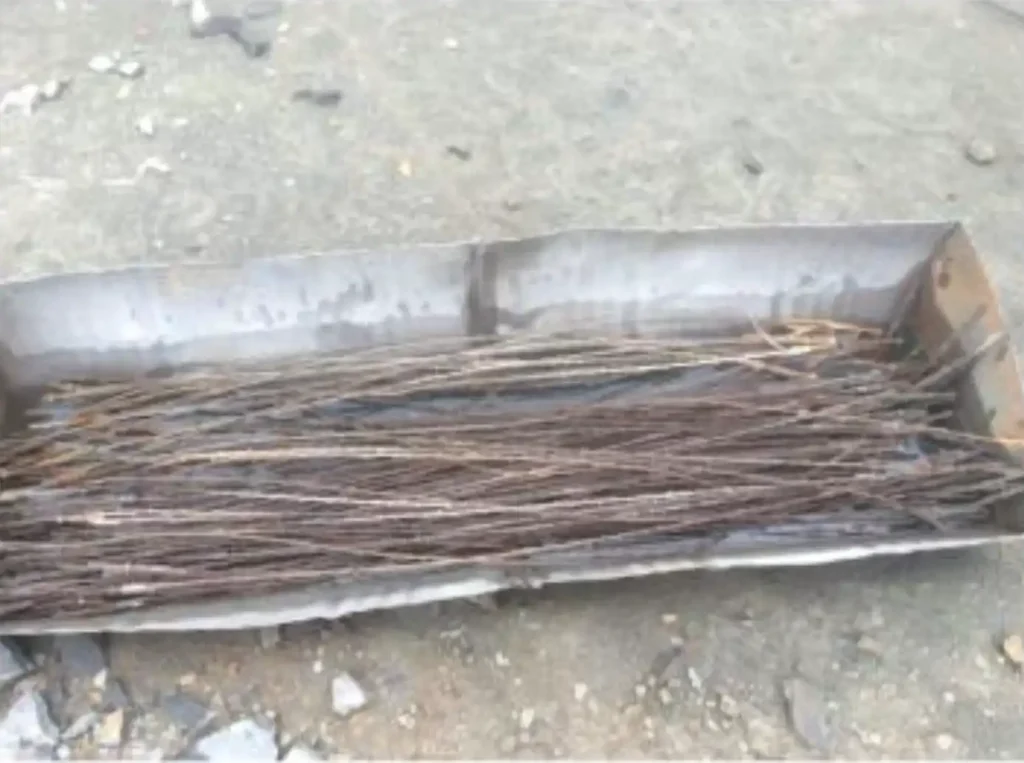
تصویر ۱۰. آمادهسازی الکترودهای دیسشارژ (کُتزدایی در حلال)
تسمه های رپینگبار و سندانیها:
با شروع طرح، تسمه به ابعاد مورد نیاز تهیه و با نقشهای که دفتر فنی تهیه کرده بود، واحد تراشکاری اقدام به سوراخکاری و آماده سازی تسمه ها نمود. فولاد چهارپهلو نیز جهت تهیه سندانی خریداری شده و به ابعاد مورد نظر برشکاری شد (تصویر ۱۱).
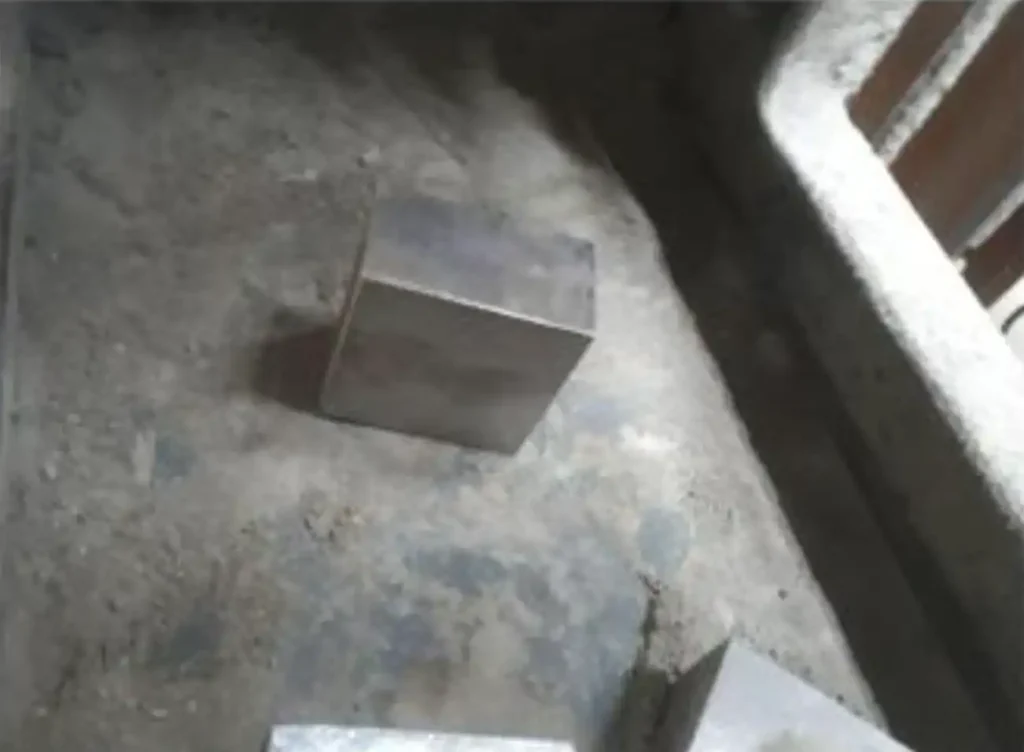
گوشواره و پین نگهدارنده صفحات:
در راستای کاهش هزینه ها تصمیم به اصلاح و استفاده مجدد از گوشواره و پینهای نگهدارنده صفحات جذب گرفته شد. بدین منظور گوشواره ها از صفحات کهنه جدا شده و با سنگ زنی اصلاح و آماده استفاده مجدد گردید (تصویر ۱۲). اشپیل موجود در سوراخ پینها نیز در آورده شده و آماده استفاده مجدد گردید (تصویر ۱۳).
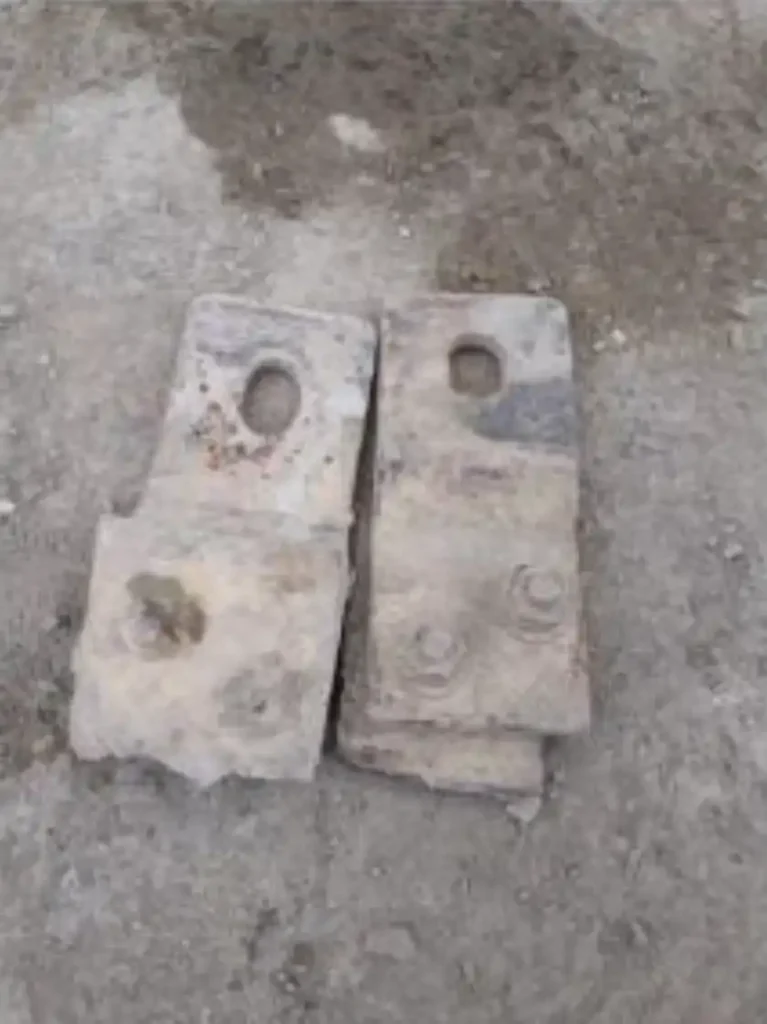
تصویر ۱۲. گوشواره های نگهدارنده صفحات جذب قبل و بعد از اصلاح و آماده سازی
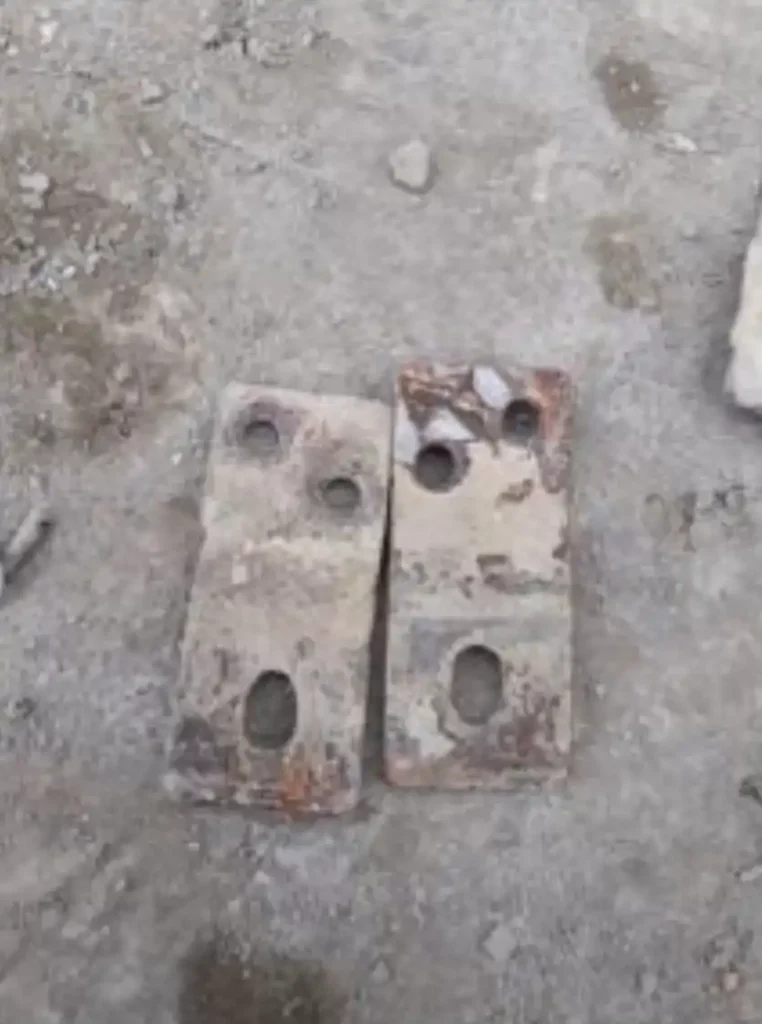
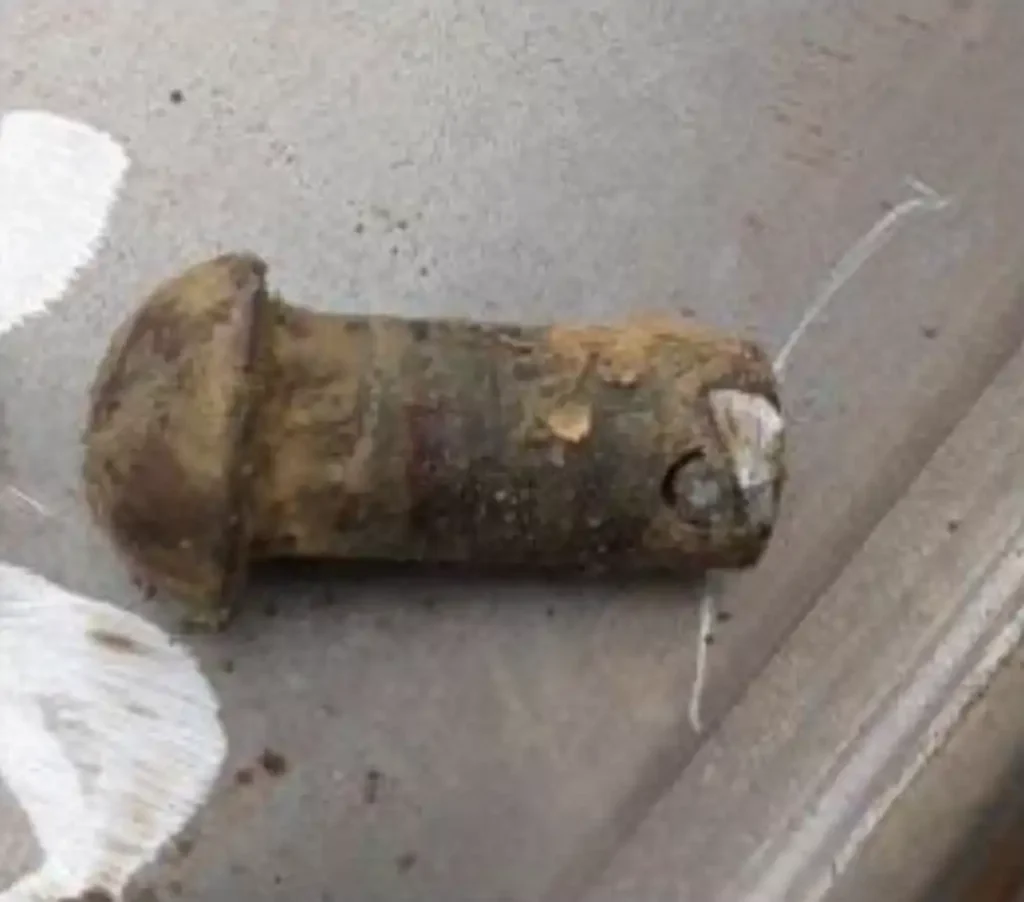
تصویر ۱۳. با در آوردن اشپیل بجا مانده درون سوراخ، پین آماده استفاده مجدد گردید.
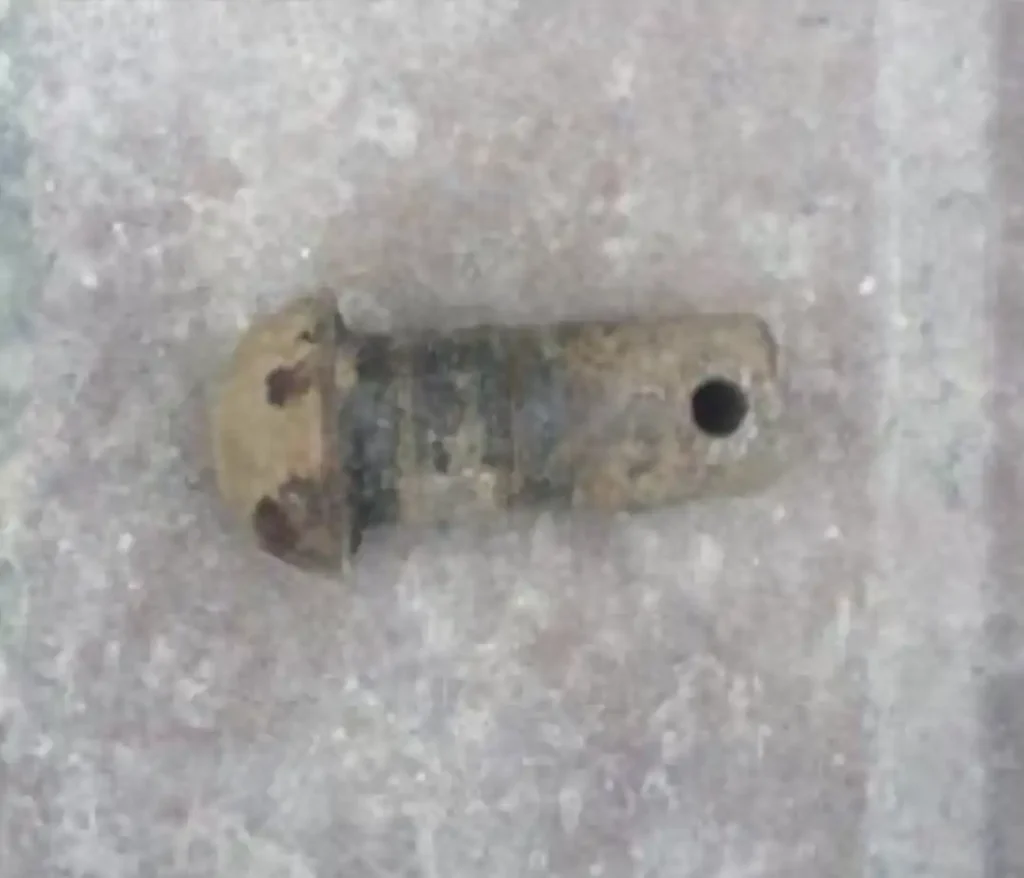
پیچ و مهره:
با برآورد انجام شده انواع پیچ و مهره به شرح جدول زیر در حین اجرای طرح خریداری و مورد استفاده قرار گرفت.
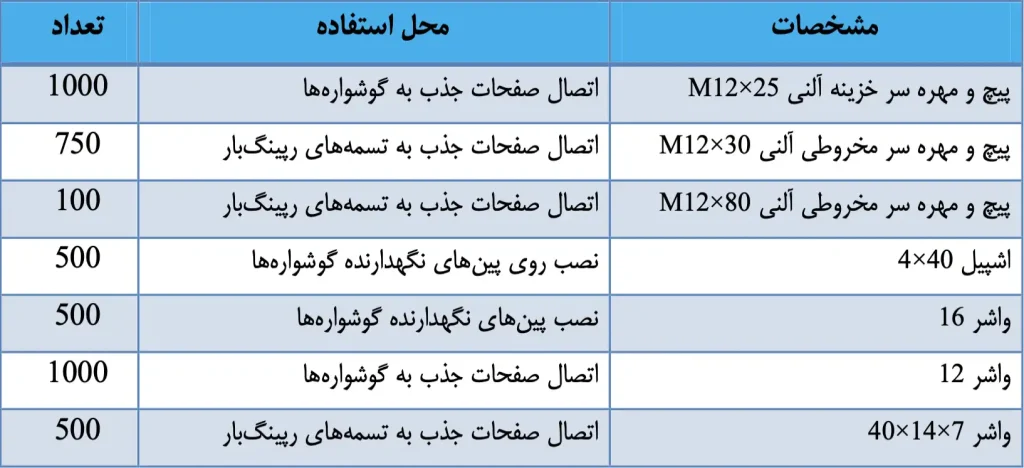
۲. برداشتن سقف الکتروفیلتر
جهت دسترسی به قطعات داخلی و تعویض آنها لازم بود تا سقف الکتروفیلتر برداشته شود. این سقف از یک صفحه جوش خورده با ضخامت ۵ میلی متر که سطح بیرونی آن عایقکاری شده و روی آن صفحات فلزی نازکی با پیچ بسته شده، تشکیل شده است. تصاویر (۱۴) تا (۱۷) مراحل نظافت، جمع آوری لایه عایق و برش صفحه سقف را نشان میدهد.
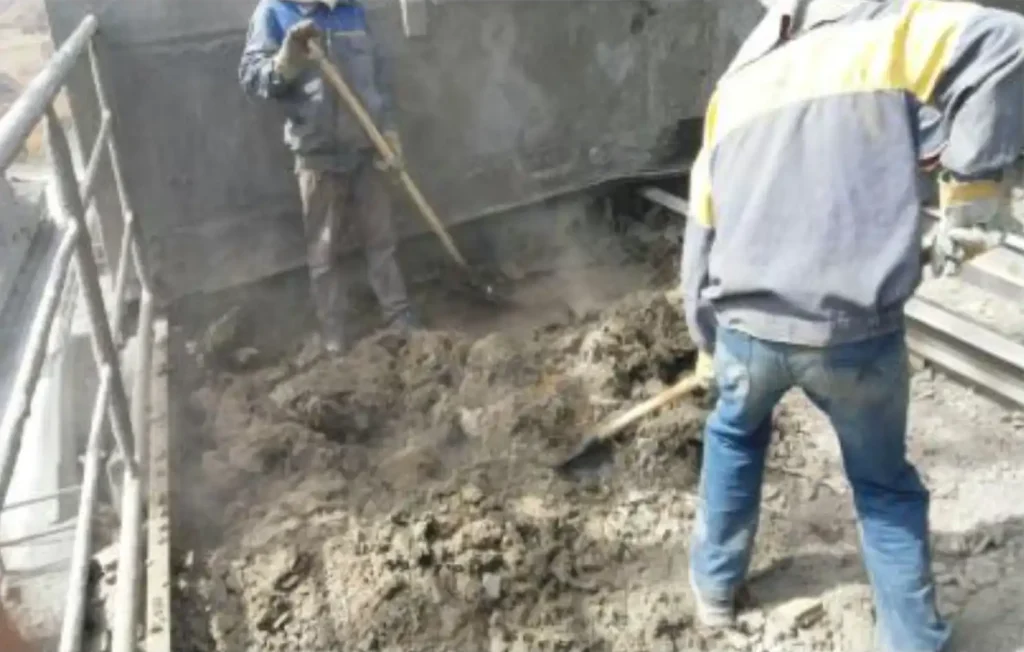
تصویر ۱۴. نظافت و جمع آوری لایه عایق روی سقف
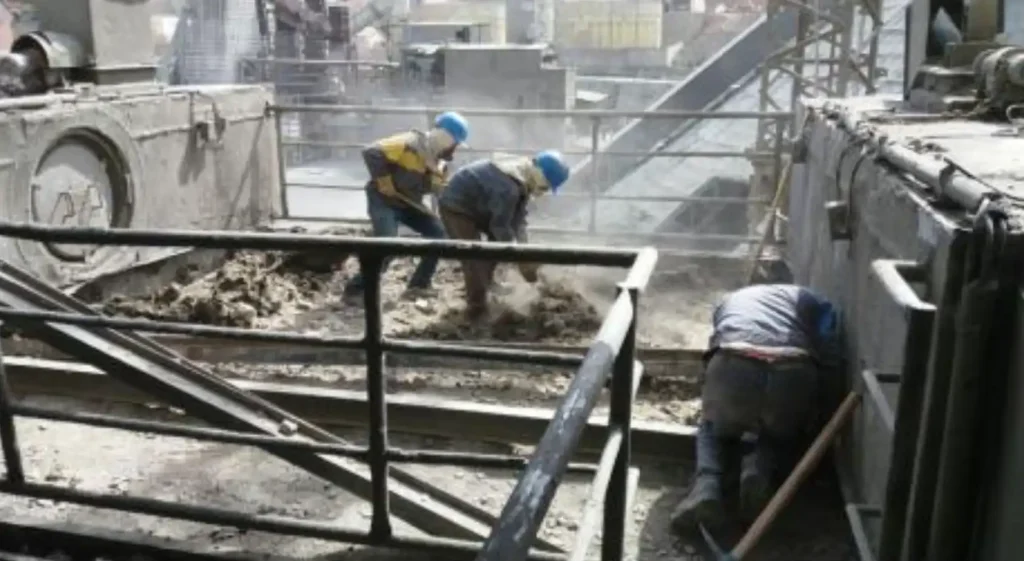
تصویر ۱۵. نظافت و جمع آوری لایه عایق روی سقف
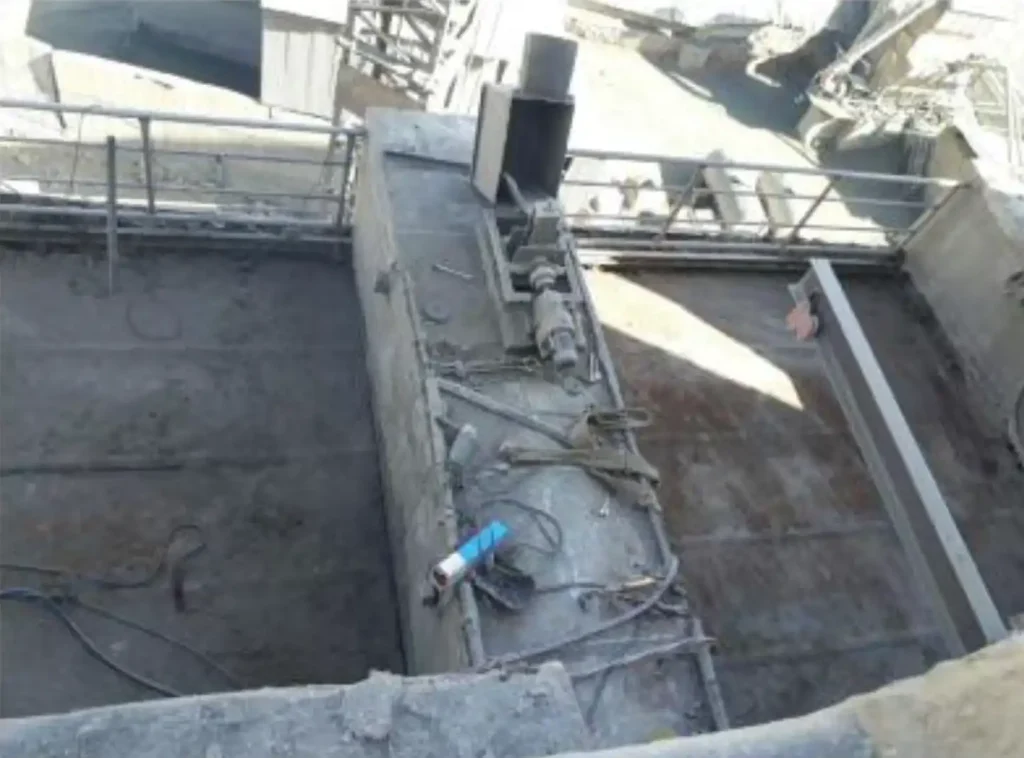
تصویر ۱۶. سقف الکتروفیلتر پس از برداشتن لایه عایق و نظافت
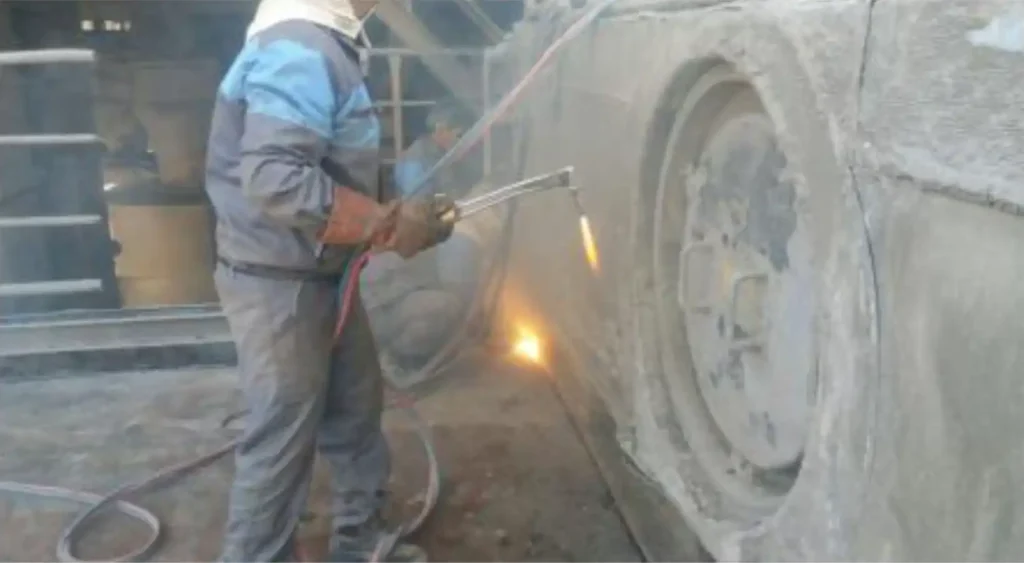
تصویر ۱۷. برشکاری صفحه خوش خورده سقف الکتروفیلتر
۳. جدا کردن رپینگبارها از صفحات
با برش پرچهای نگهدارنده صفحات به رپینگبارها، صفحات از رپینگبارها جدا شدند (تصویر ۱۸).
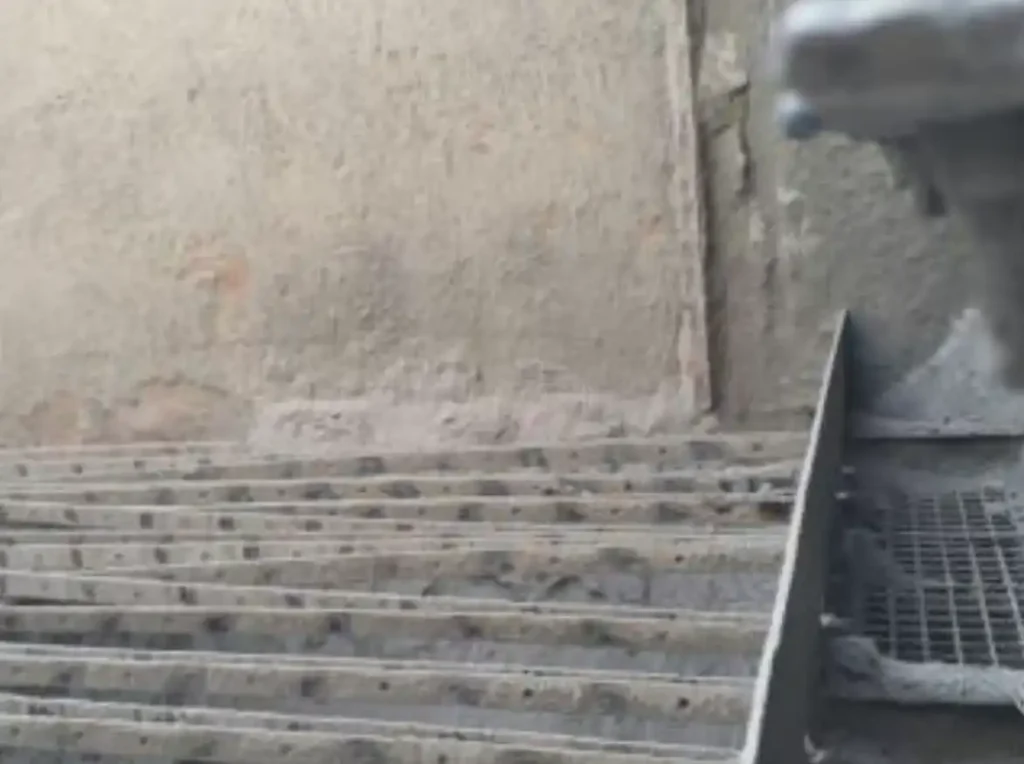
تصویر ۱۸. تسمه های رپینگبار. اتصالات پرچ جدا شده و صفحات جذب بیرون آورده شده است.
۴. بیرون آوردن صفحات جذب
از آنجا که اکثر صفحات از محل اتصال به گوشواره ها دچار شکستگی بودند، آنها را با سیم مفتول به شاسی صفحات بسته تا مهار شوند و در حین انتقال توسط تاور از شاسی جدا نشوند (تصویر ۱۹).
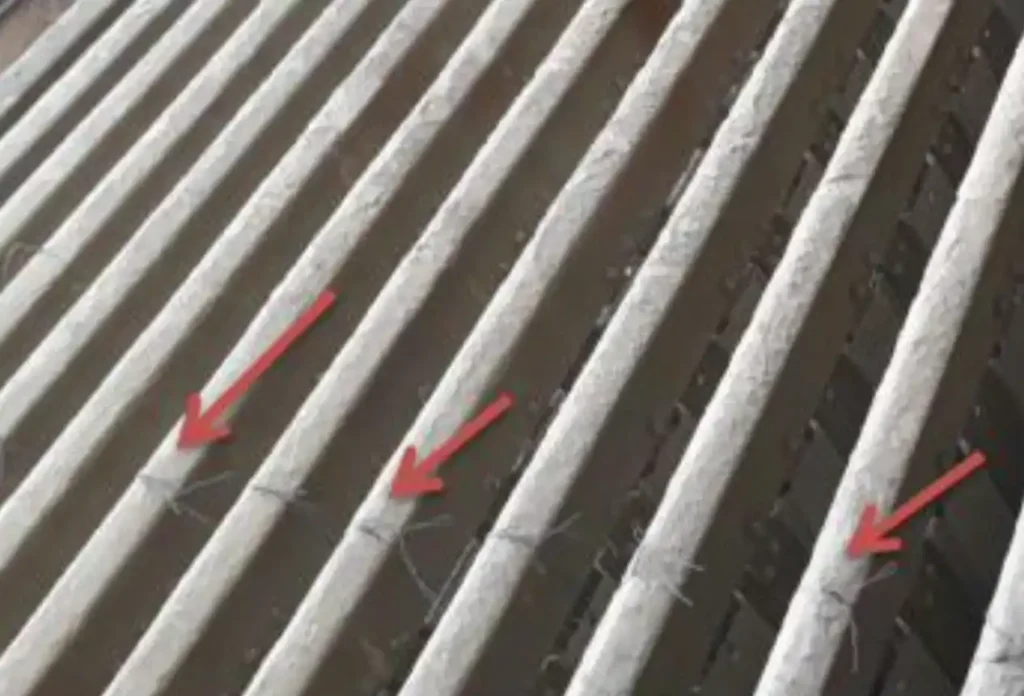
تصویر ۱۹. مهار صفحات جذب به شاسی با سیم مفتول. این کار برای تمام صفحات انجام شد.
کار انتقال صفحات به محیط بیرون توسط تاور موجود در کنار الکتروفیلتر انجام شد (تصویر ۲۰).
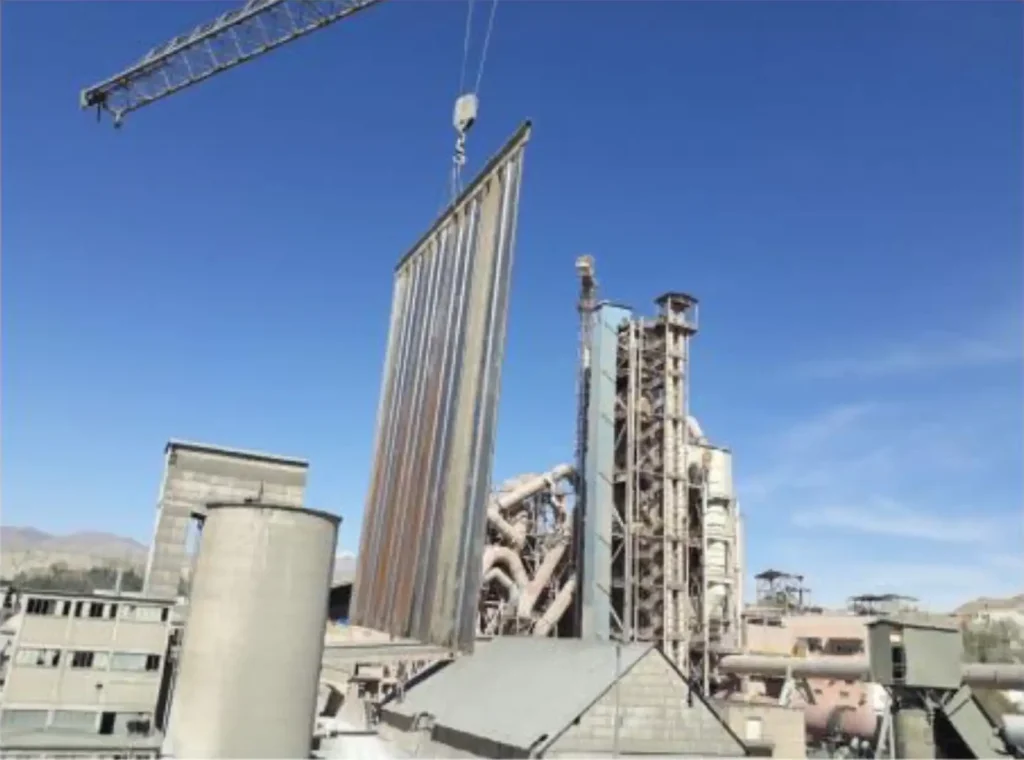
تصویر ۲۰. جابجایی صفحات جذب توسط تاور
۵. جدا کردن صفحات ازگوشواره ها و شاسی
به منظور تعویض صفحات جذب، کلیه صفحات از شاسی و گوشواره ها جدا گردید (تصویر ۲۱).
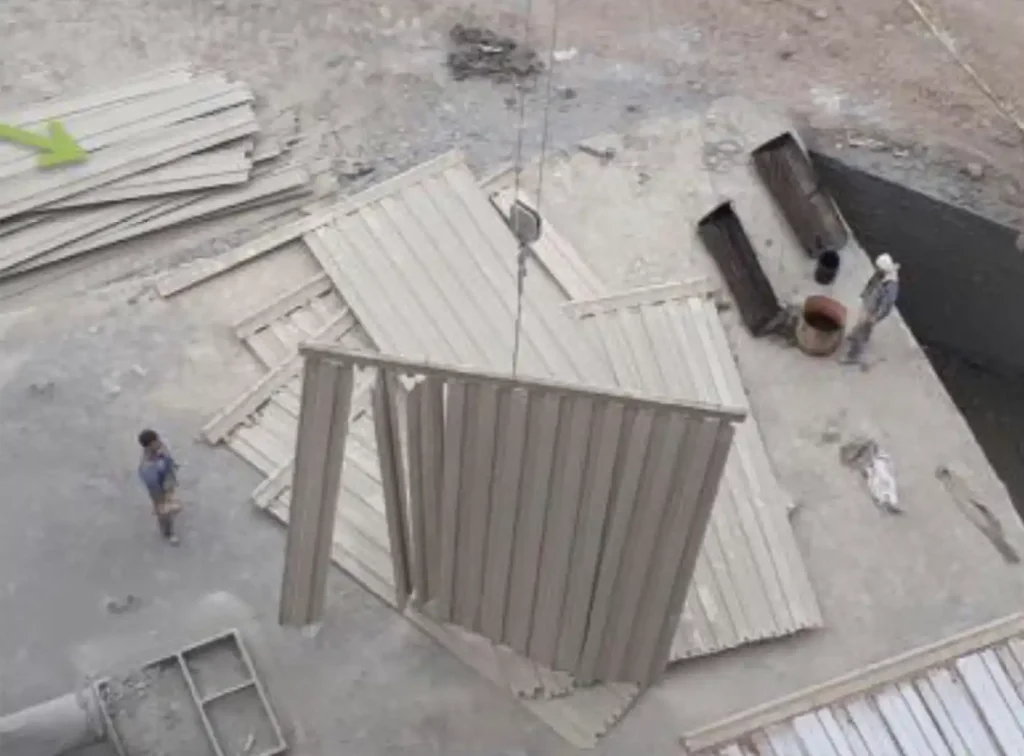
تصویر ۲۱. جدا سازی صفحات از شاسی
۶. بیرون آوردن الکترودهای دیسشارژ
پس از بیرون آوردن صفحات جذب، مشاهده شد که الکترودهای دیسشارژ و شاسی آنها نیز وضعیت نامناسبی دارد که بدلیل حجم بالای کار تصمیم گرفته شد تمامی آنها را نیز به بیرون منتقل کرده و عملیات ترمیم روی آنها انجام گیرد (تصویر ۲۲).
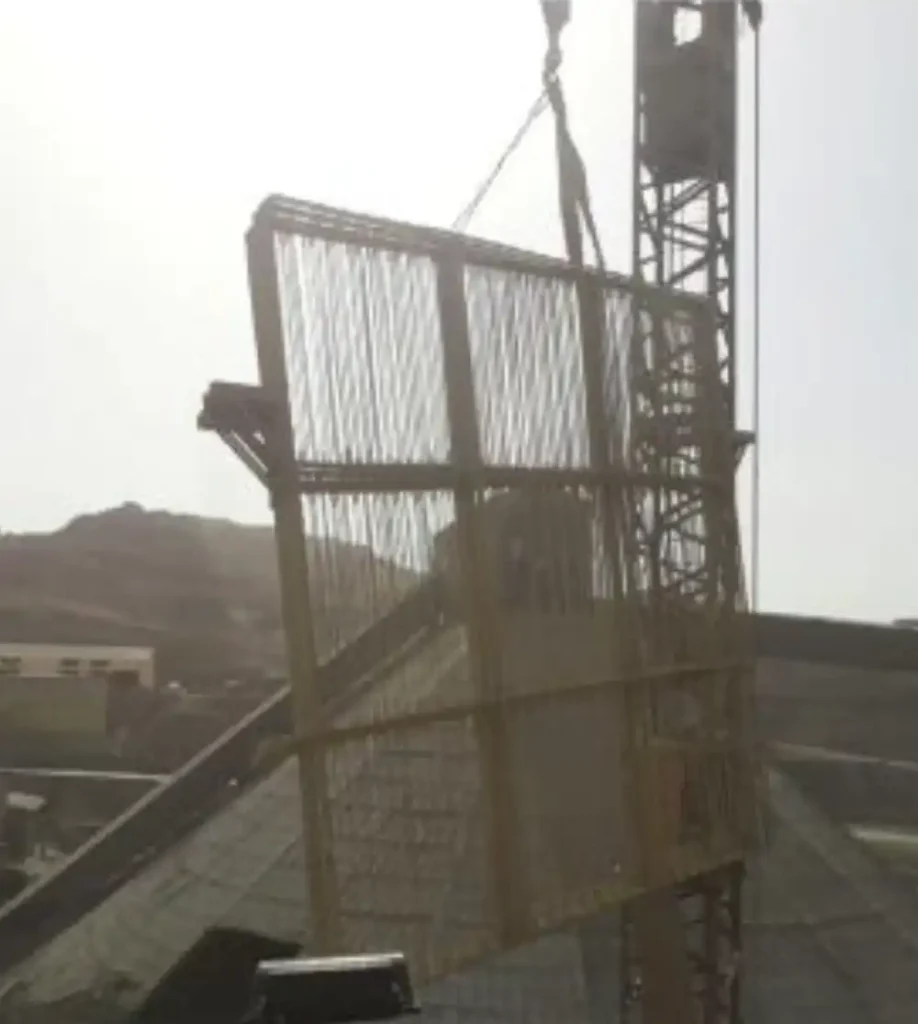
تصویر ۲۲. انتقال الکترودهای دیسشارژ به بیرون
۷. ترمیم شاسی و الکترودهای دیسشارژ
تصاویر (۲۳) تا (۲۶) عملیات ترمیم شامل اصلاح شاسی، نظافت کامل الکترودها، تعویض الکترودهای معیوب و نصب الکترود در محلهای فاقد الکترود را نشان میدهد.
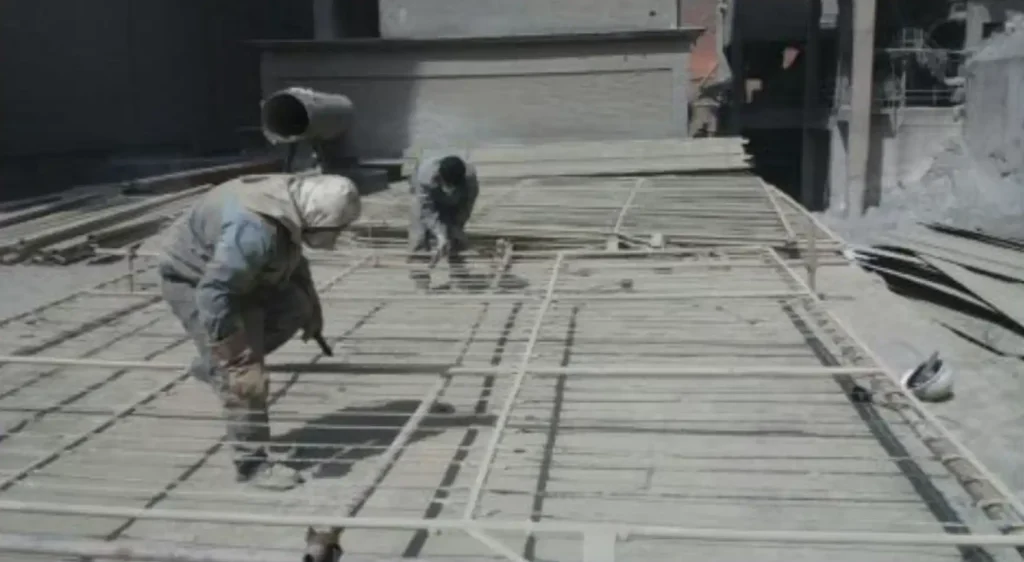
تصویر ۲۳. نظافت الکترودهای دیسشارژ توسط برس سیمی
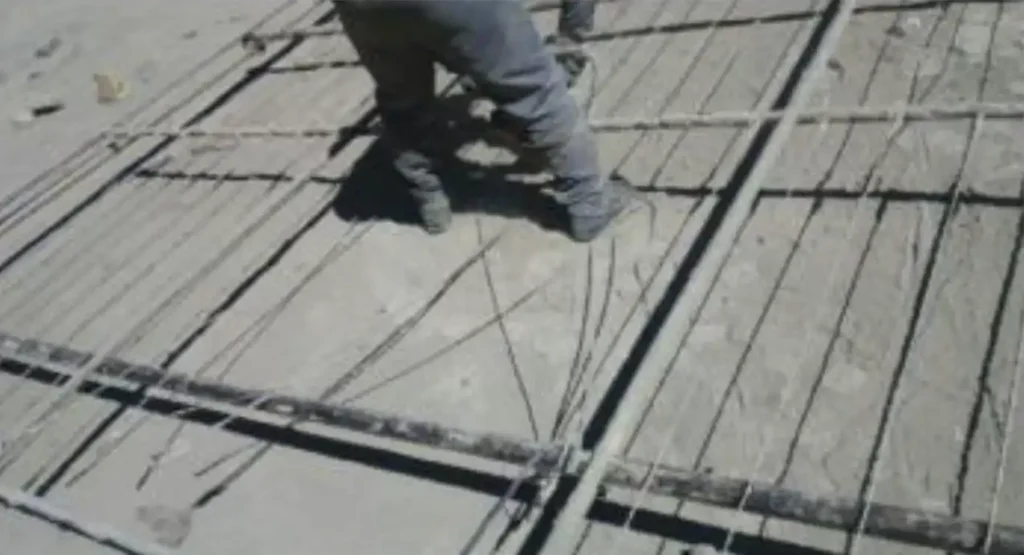
تصویر ۲۴. بریدن و جداسازی الکترودهای معیوب و شل شده
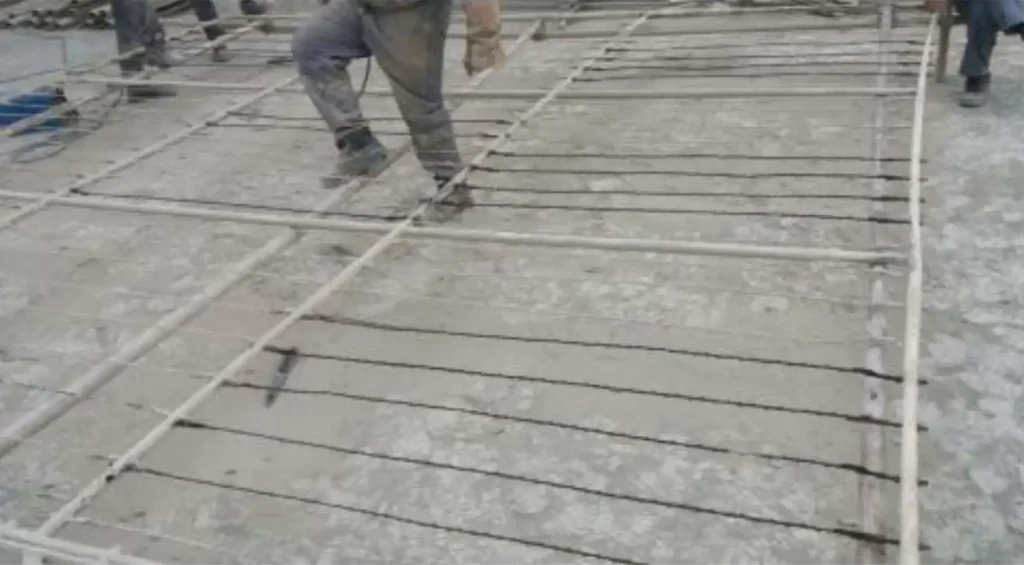
تصویر ۲۵. نصب الکترودهای جدید روی شاسی
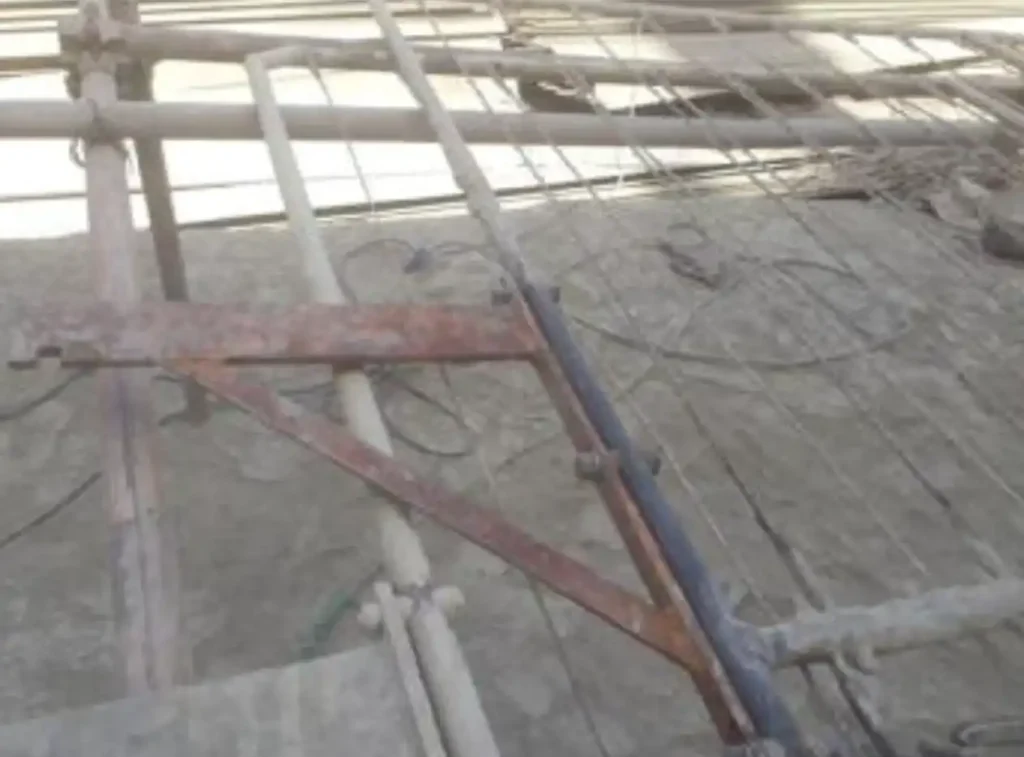
تصویر ۲۶. ترمیم و تعویض بخشهای آسیب دیده شاسی الکترودهای دیسشارژ
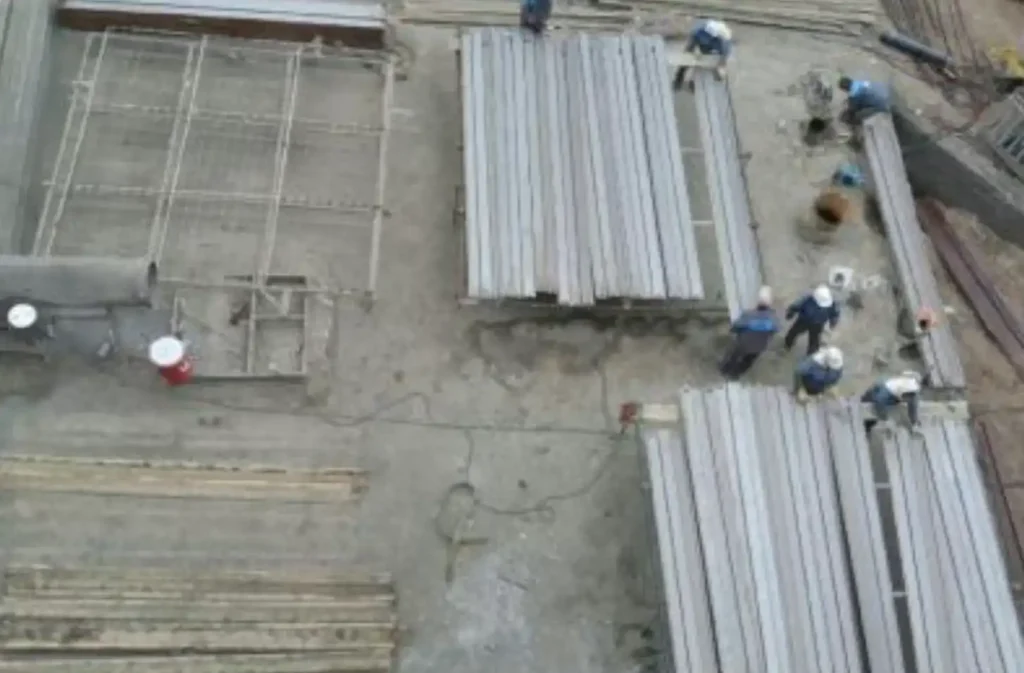
تصویر ۲۷. مونتاژ صفحات جذب
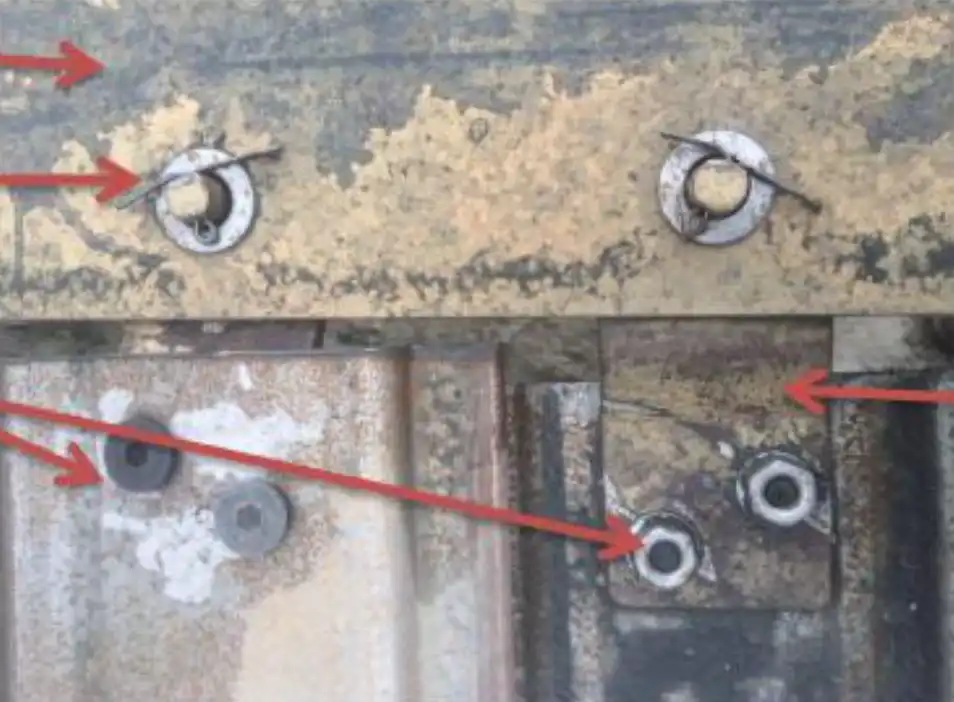
تصویر ۲۸. نحوه مونتاژ و اتصال صفحات جذب به گوشواره ها و شاسی
۹. نظافت کامل بدنه داخلی
با بیرون آوردن تمامی صفحات جذب و الکترودهای دیسشارژ امکان نظافت بدنه داخلی الکتروفیلتر فراهم شد. به جهت کارکرد طولانی و رطوبت موجود در هوای ورودی، لایه مستحکمی از مواد (کُت گرفتگی) که در بخشهایی ضخامت آن به حدود سی سانتیمتر هم میرسید، ایجاد شده بود که این لایه های مواد بطور کامل پاکسازی و به بیرون دستگاه منتقل گردید. در جریان نظافت علاوه بر سطح بدنه، کلیه چکشها، شفتها و توريهای کانال ورودی نیز نظافت گردید تصاویر (۲۹) تا (۳۲)).
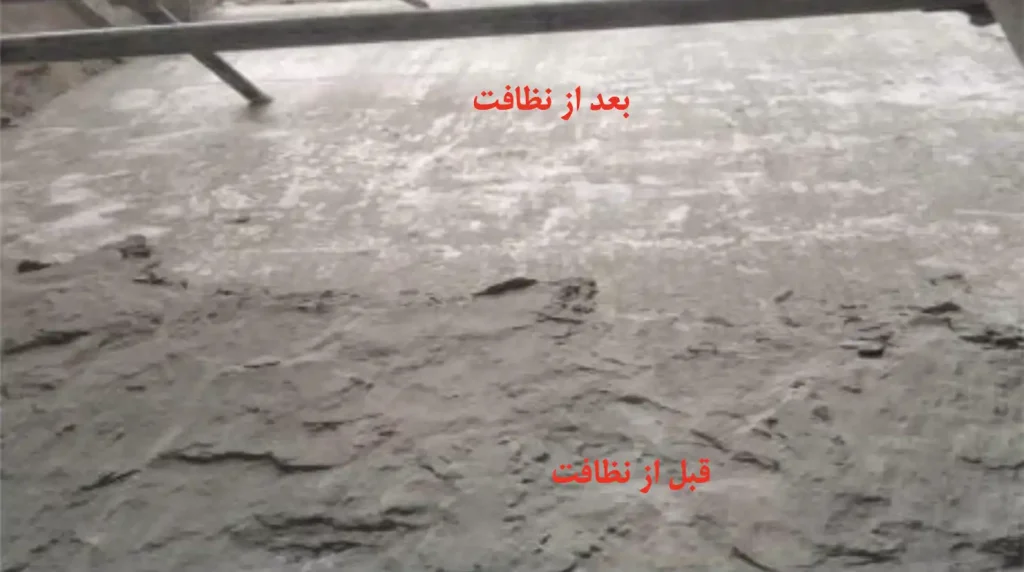
تصویر ۲۹. نظافت کامل بدنه داخلی الکتروفیلتر
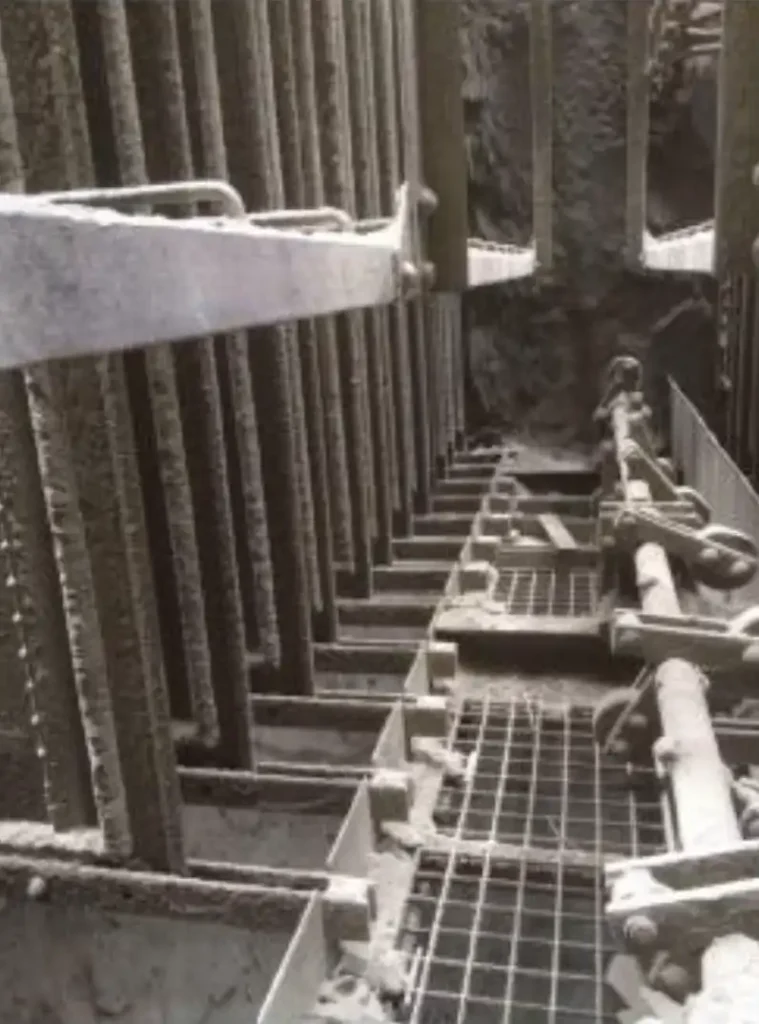
تصویر ۳۰. سیستم ضربه زن قبل و پس از نظافت
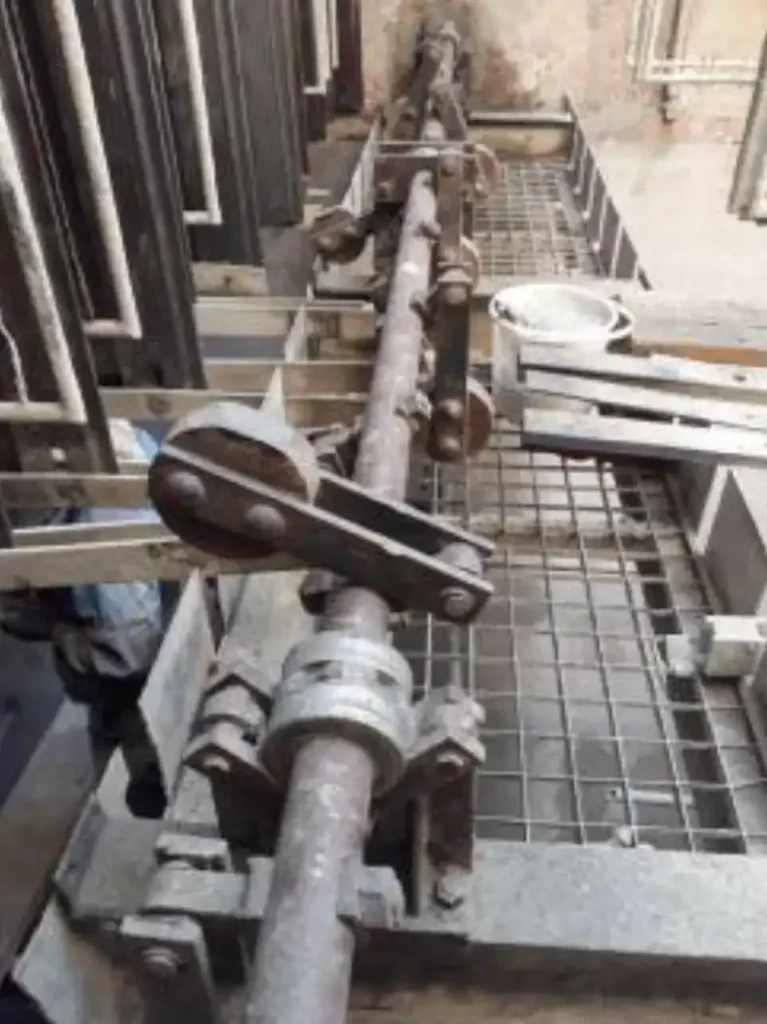
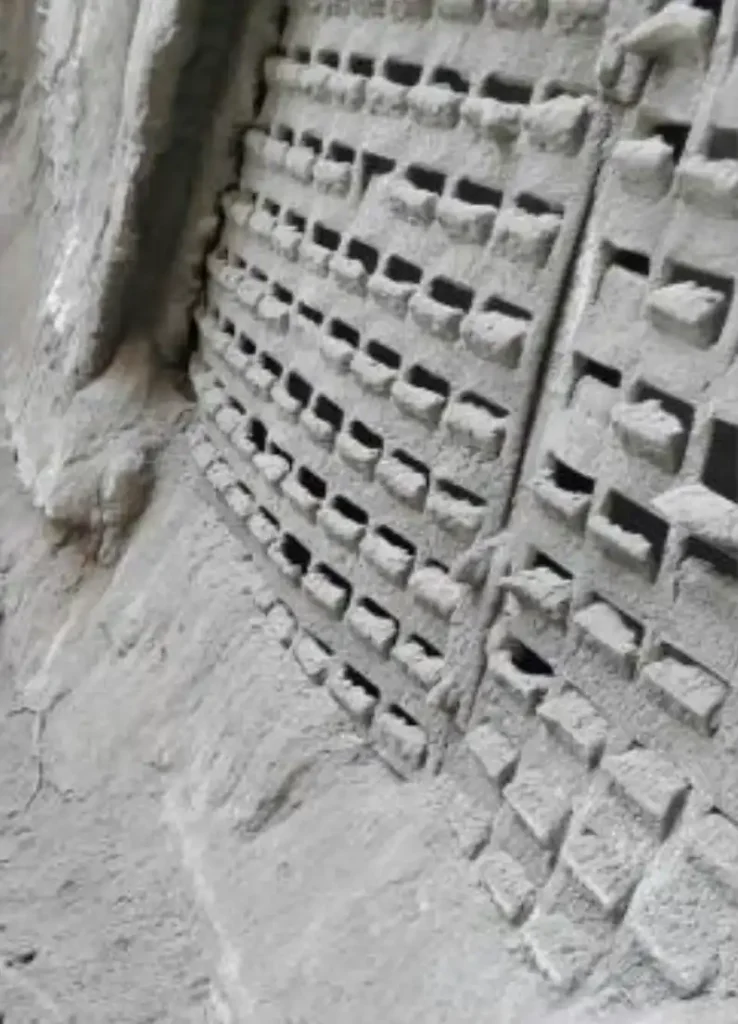
تصویر ۳۱. توری ورودی الکتروفیلتر قبل و بعد از نظافت
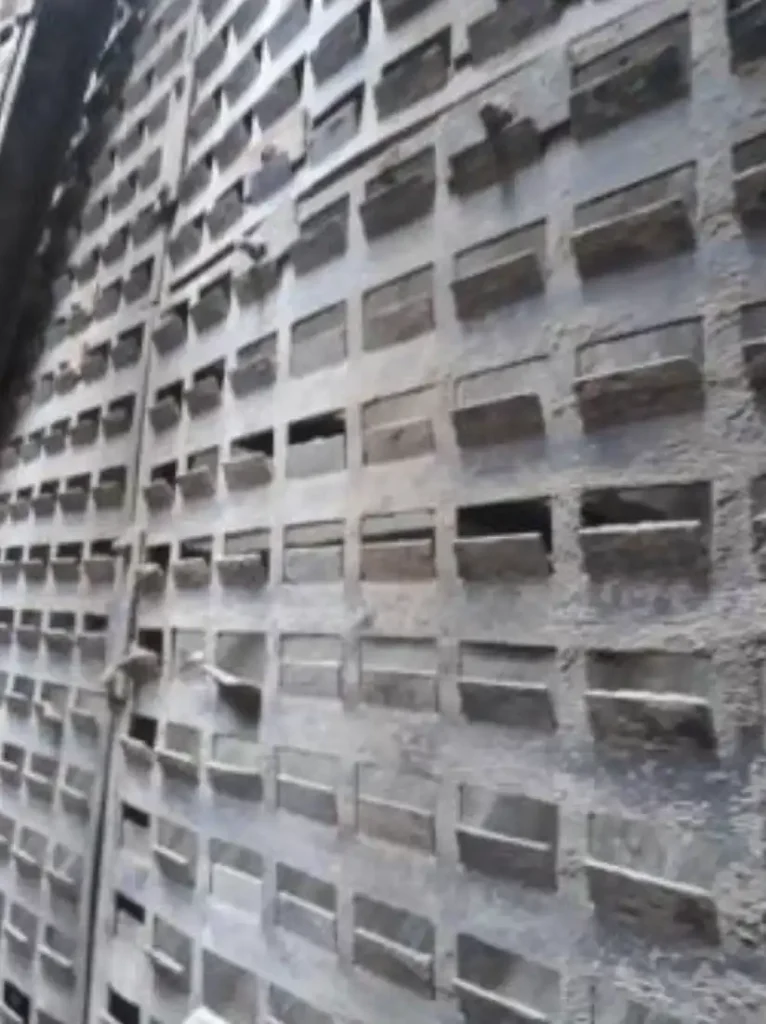
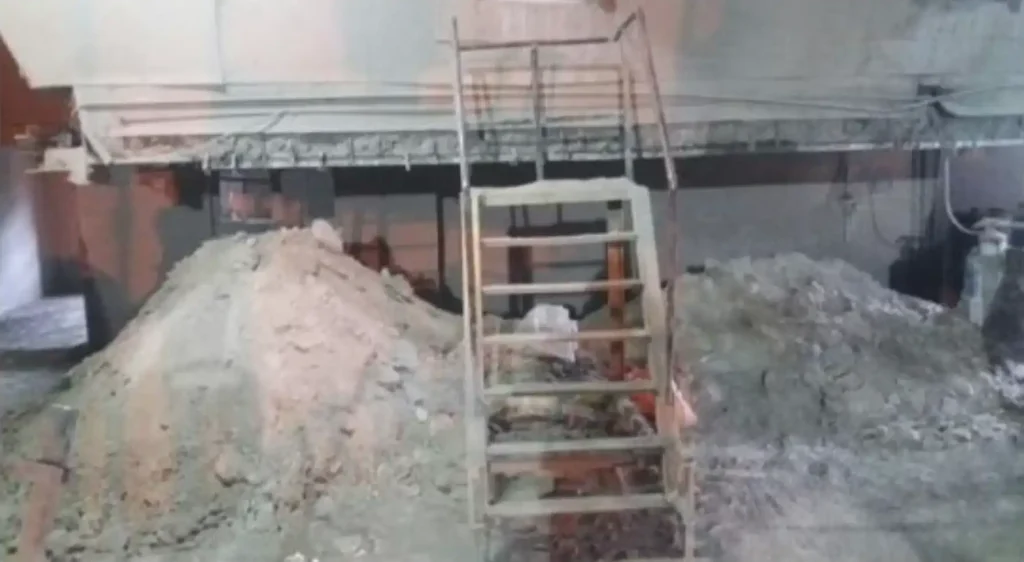
تصویر ۳۲. ضایعات تخلیه شده از داخل الکتروفیلتر پس از نظافت و کتزدایی
۱۰.مونتاژ اجزای داخلی
با ترمیم و تعویض الکترودها و صفحات جذب، شاسی صفحات (تصویر ۳۳) و الکترودها (تصویر ۳۴) توسط تاور به داخل دستگاه منتقل و در جای خود مستقر گردید. پس از استقرار صفحات جذب، تسمه هاي رپینگبار نیز به داخل دستگاه منتقل و توسط پیچ و مهره به سوراخهای قسمت پایینی صفحات متصل گردید (تصویر ۳۵). سپس سندانیها روی تسمه های رپینگبار جوشکاری شد (تصویر ۳۶). شاسی الکترودهای دیسشارژ نیز روی قلابهای نگهدارنده خود مستقر گردید.
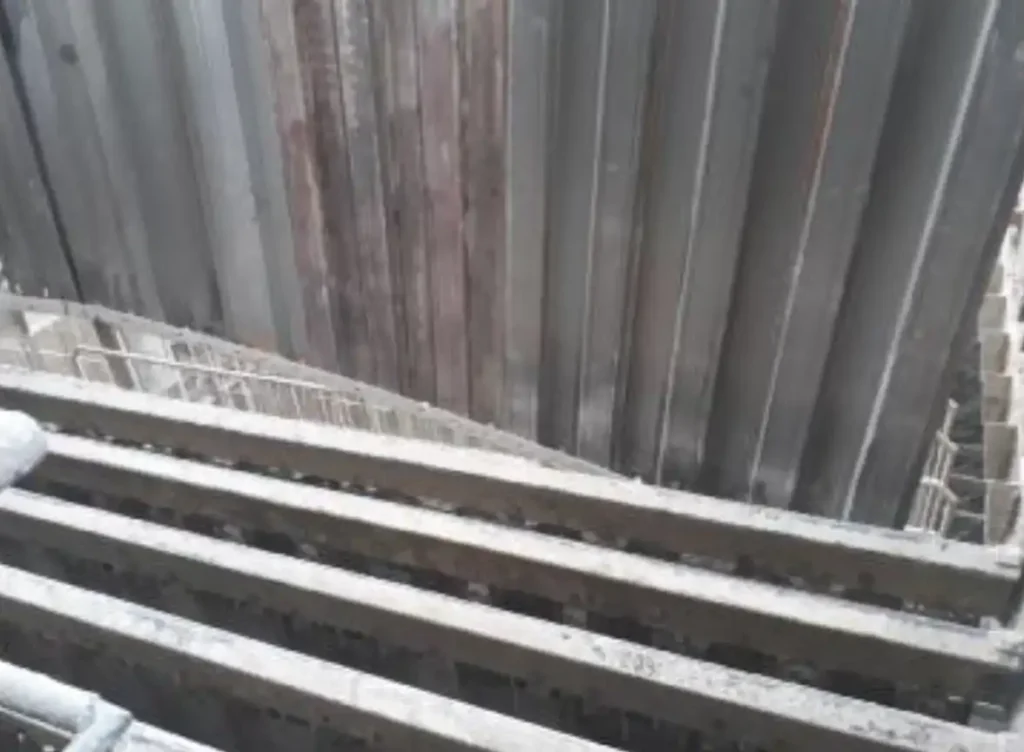
تصویر ۳۳. نصب مجدد شاسی صفحات جذب پس از تعویض صفحات
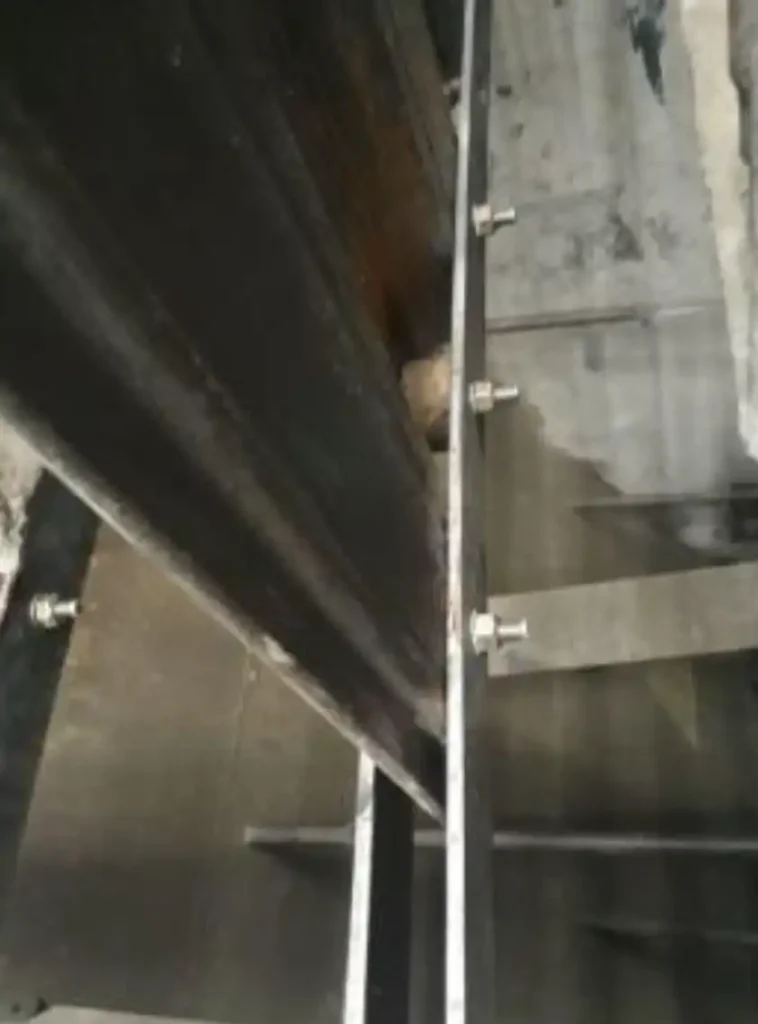
تصویر ۳۵. اتصال صفحات جذب به تسمه های رپینگ بار توسط پیچ و مهره
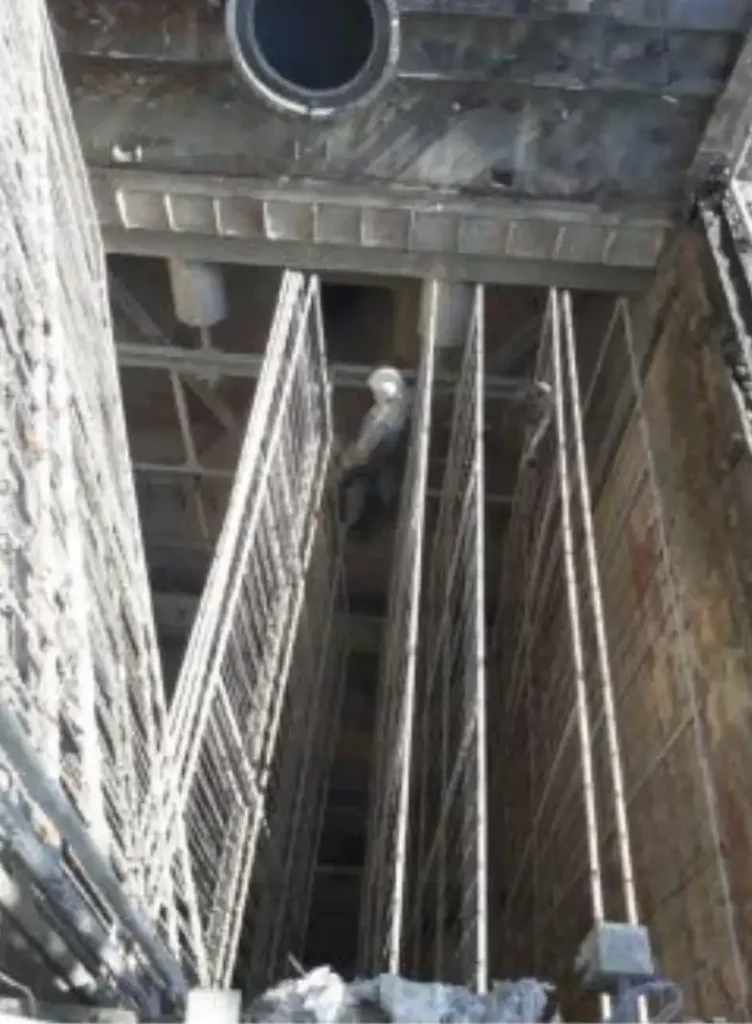
تصویر ۳۴. نصب مجدد شاسی الکترودهای دیسشارژ پس از ترمیم
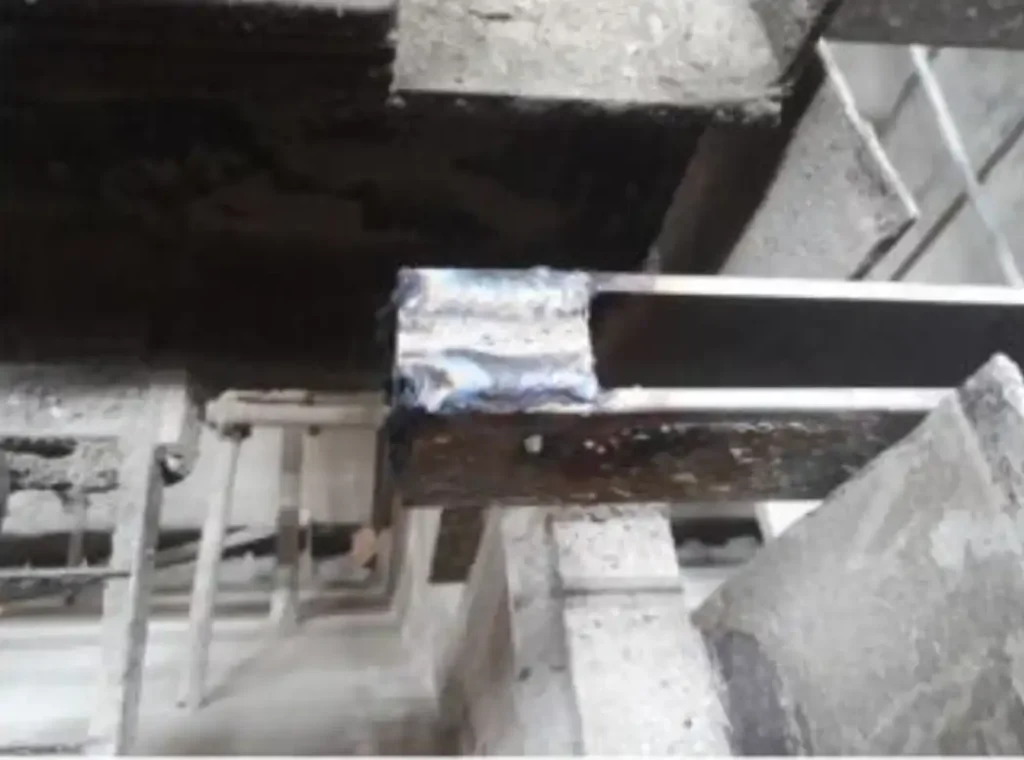
تصویر ۳۶. اتصال (جوشکاری) سندانی به تسمه های رپینگبار
۱۱. نصب سقف
پس از پایان عملیات نصب شاسی صفحات جذب و الکترودهای دیسشارژ داخل الکتروفیلتر، عملیات نصب سقف (تصویر ۳۷) و عایقکاری آن با استفاده از عایق پشم سنگ به ضخامت ده سانتیمتر انجام شد و در انتها لایه آخر که صفحات فلزی به ضخامت ۲ میلیمتر بود جهت حفاظت از لایه عایق نصب گردید (تصویر ۳۸).
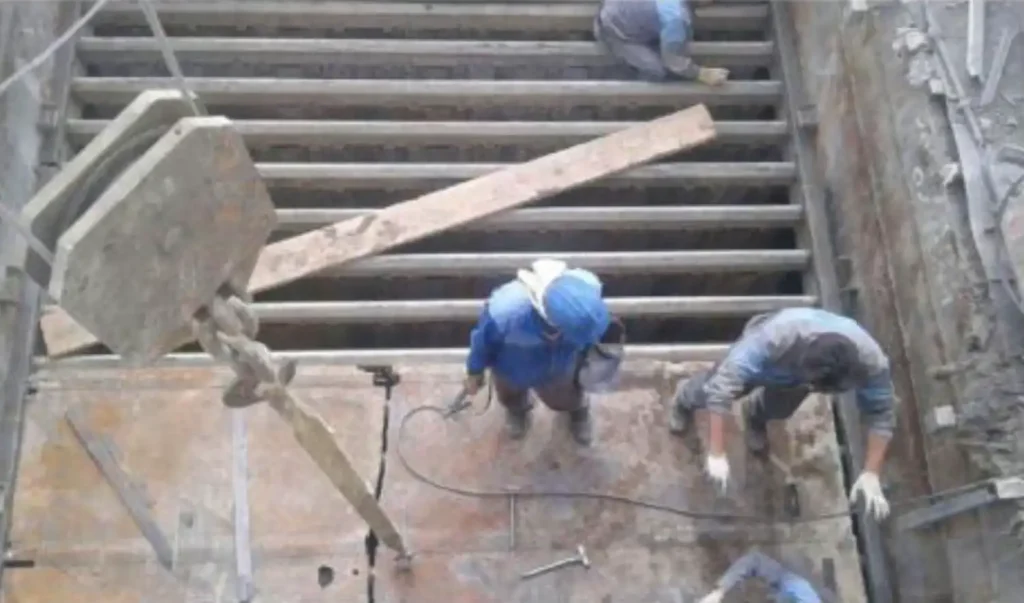
تصویر ۳۷. نصب صفحات سقف
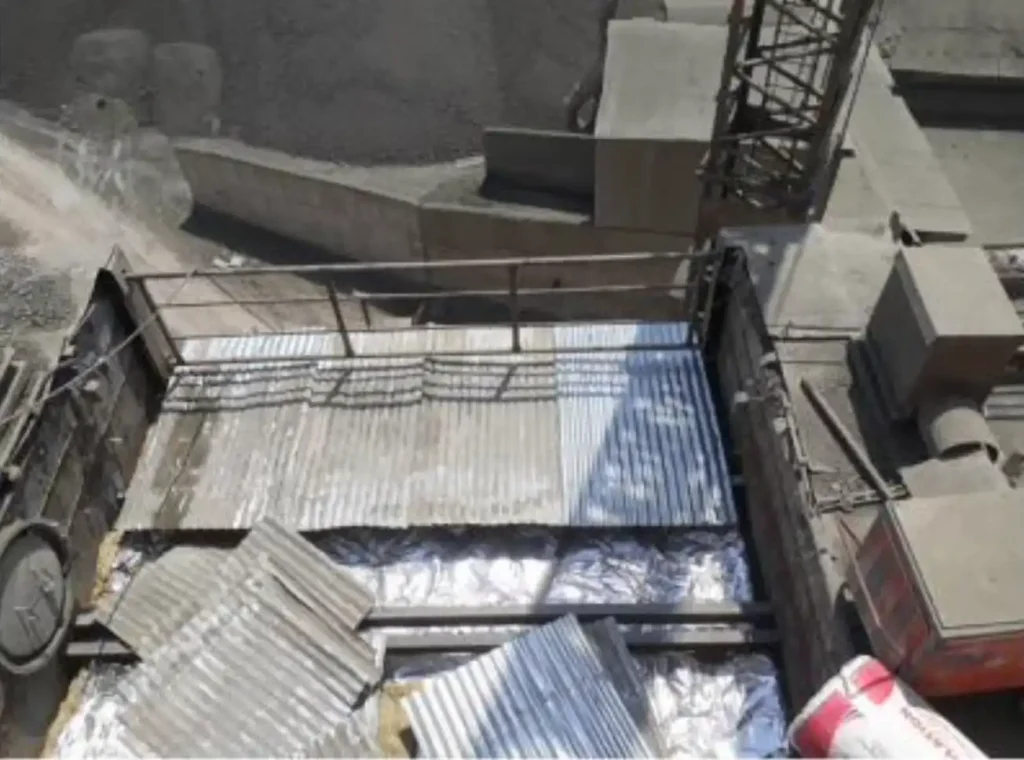
تصویر ۳۸. نصب عایق پشم سنگ روی سقف
۱۲. کت زدایی و تست فن
به منظور اطمینان از عملکرد مطلوب فن الکتروفیلتر، لایه کت ایجاد شده روی پروانه فن زدوده شد و با استارت فن، ارتعاش و بالانس آن ارزیابی شد که در وضعیت مطلوبی قرار داشت (تصویر ۳۹).
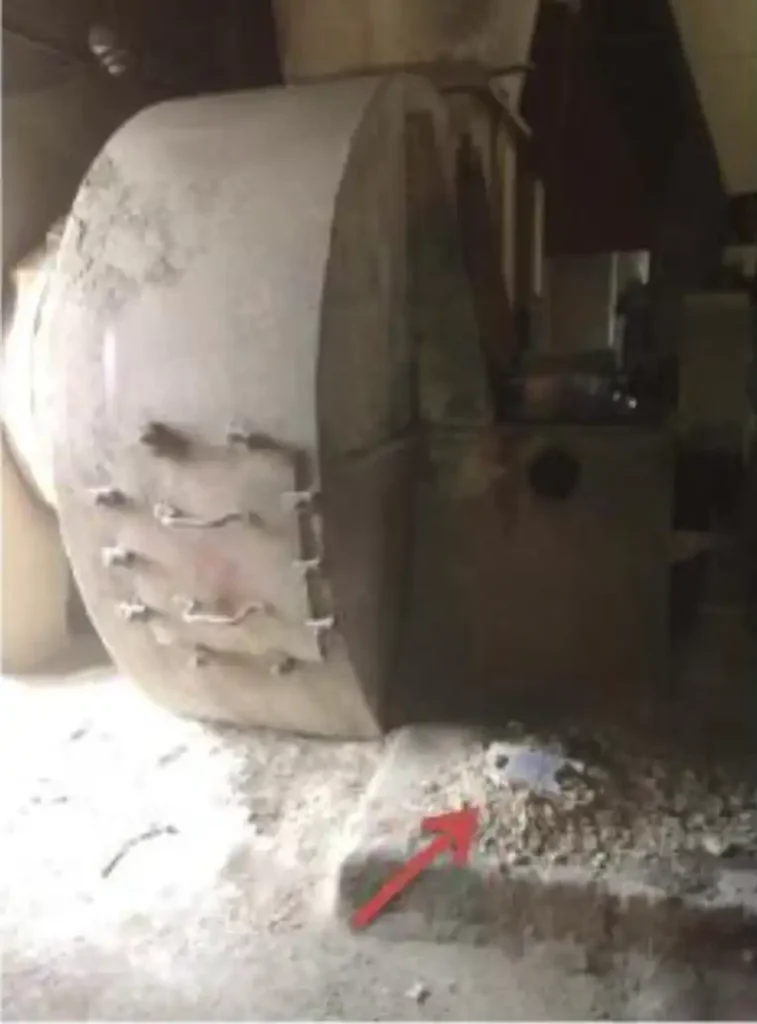
تصویر ۳۹. کت زدوده شده از روی پروانه فن
۱۳. تست سرد و راه اندازی نهایی
پس از پایان کار و نصب سقف، تمامی قسمتهای الکتروفیلتر بازدید شده و دربها بسته شد. در انتها به منظور اطمینان از عدم ایجاد اتصالی و تشکیل میدان الکتریکی مناسب و بالا رفتن شدت جریان، تست سرد صورت پذیرفت که شدت جریان و ولتاژ میدان الکتریکی داخل دستگاه در وضعیت مطلوبی (میلی آمپر به ۳ برابر قبل از تعمیرات افزایش یافته است)
گرفت (تصویر ۴۰). پس از اطمینان از عدم وجود مشکل خاصی بر روی دستگاه، آسیاب استارت شده و الکتروفیلتر در وضعیت کار واقعی نیز بدون مشکل، عملکرد مطلوبی داشت.
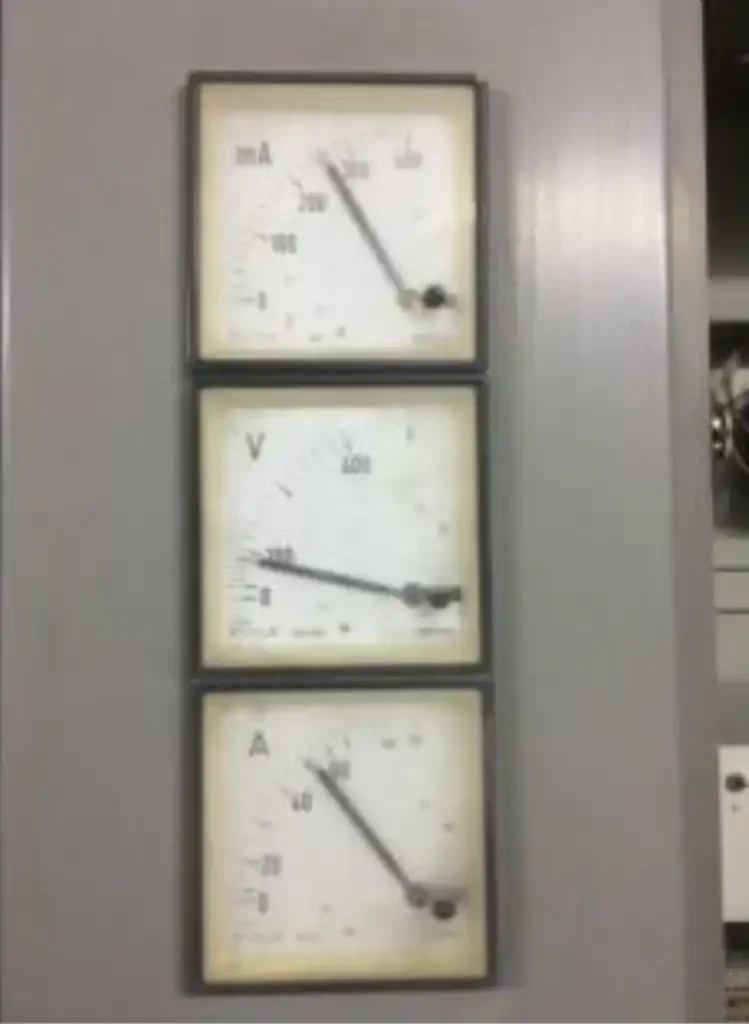
تصویر ۴۰. تست سرد الکتروفیلتر
۱۴.اقدامات اصلاحی:
طبق مدارك موجود در مدارات فرمان برق در خصوص نحوه استارت و بررسی اینترلاك استارت ادوات مجموعه لورگی آسیاب سیمان ۴ (مارپیچ، چکش ها، هاي ولتاژ)، پس از استارت مارپیچ زمینی فن الکتروفیلتر استارت می گردید، لیکن استارت مجموعه ادوات لورگی طبق کلیدهای موجود بر روی میز کنترل در دسترس اپراتور قرار داشت و این مهم همواره توسط بهره بردار انجام می پذیرفت که البته در صورت عدم استارت این مجموعه در طول مدت ۲۰ دقیقه فرمان استوپ به آسیاب صادر می گردید ( این تایم جهت فراهم شدن زمان لازم جهت رفع اشکال بوده که گاها در این مدت مواردی مانند رفع گیر مارپیچ زیر الکتروفیلتر و روتاری و .. مانع از استوپ آسیاب می گردد)؛ در حال حاضر برای حصول اطمینان از استارت این مجموعه در زمان استارت آسیاب در حال حاضر مدار فرمان لورگی به نحوی تغییر داده شده است تا در زمان استارت اولین بخش از لورگی )مارپیچ زیر الکتروفیلتر( الباقی المان ها )چکش ها و های ولتاژ( به صورت خودکار استارت شوند و نیازی به استارت چکش ها و های ولتاژ به صورت جداگانه نباشد. همچنین پس از توقف الکتروفیلتر، سیستم های ضربه زن که زمان ضربه زدن آنها نیز تغییر یافته است به مدت ۱۸۰ دقیقه در مدار می باشند.
آخرین مطالب
جدیدترین اخبار و رویدادهای شرکت سیمان شمال